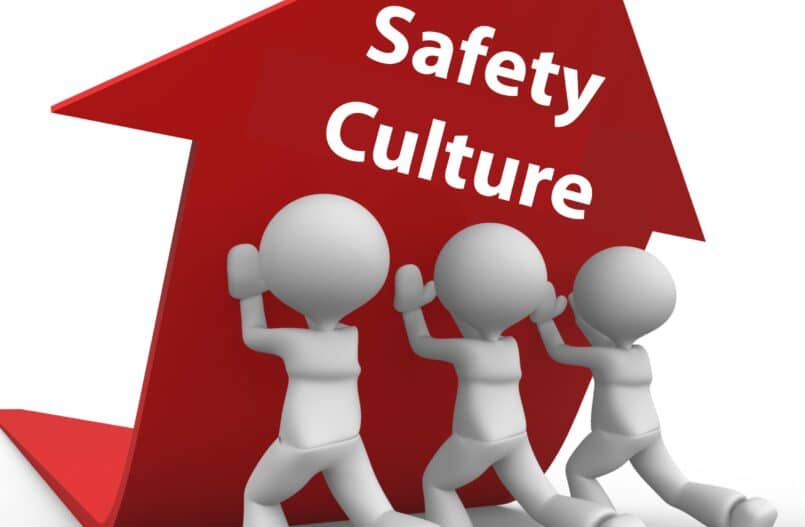
Feature article: Creating a participation-based safety culture
Submitted by:
Andrew Warmington
Sarah Ingle, who specialises in chemical safety and regulatory compliance at EcoOnline, explores how chemists can create a participatory safety culture
With news of Monkeypox’s emergence and possible mutation to become seen as the latest worrying infectious disease, I am reminded of shocking revelations in The Times last year. It divulged that there have been over 100 safety breaches at UK laboratories handling dangerous pathogens, over the past 15 years. Lapses included a worker being bitten by an infected ferret at Porton Down, the government’s high security research facility, and employees being exposed to TB bacteria.
While major viral leaks have been avoided, there clearly have been slip-ups. Considering the potential harm to human health that can result from these types of errors this does underline the need for constant vigilance and the need for robust safety procedures, and more importantly the creation of a positive safety culture.
Most of us, if we make a mistake, won’t release a potential pandemic on the world. But when working with hazardous substances we can still injure ourselves or others. Creating a positive safety culture I spent some of my earlier career in construction and spent time on sites where I saw things happen that would be unacceptable today.
The situation has vastly improved today, due to a deeply embedded culture change delivering a safer working environment. While lab-based work is very different in its nature, there are still potentially grave risks to health. Every organisation has, or should have, a safety culture. This can be positive or negative, depending on whether it has developed and implemented correctly within an organisation.
When incidents arise, it is because the existing culture is ineffective at keeping people safe from harm. Transforming this situation to achieve something fit-for-purpose requires consistency and an ongoing, targeted approach. Change takes time and requires constant communication and message reinforcement to people at all levels.
Inspire
We have all experienced tedious health and safety memos, briefings or posters, which are too often boring and jargon-heavy. While this is ticking the box, no-one’s behaviour will be changed. Frequently they opt for a ‘tell’ approach rather than looking to persuade.
There are seven principles of persuasion, which were devised by Cialdini: reciprocity, scarcity, authority, commitment, consistency, liking and consensus. By understanding these, you can use them to create a participation based safety culture. What works is being engaging, so be visual, be funny and use the unexpected.
While the topic is serious, you can still adopt a light touch. For example, Total Energy in Denmark made humour a core component in their behavioural safety campaign ‘don’t be a dummy’ which showed a crash test dummy undergoing various experiences which would maim or kill a human.1
Using humour creates a bonding experience which makes attitudinal shift possible and longer-lasting. It is tempting to regard H&S protocols as solely a lab matter. While this is important, the other teams, including senior management, play an important role as culture is set from the top. A recent HBR study shows that companies facing financial pressures saw higher levels of workplace accidents, as corners were cut to save money.2
So, the C-Suite should also beware of the unintended consequences of decisions made at board level. Leaders have to walk the walk, modelling excellent safety behaviour at all times. If we look to other industries e.g. heavy equipment manufacturing, many (rightly) ensure that office staff have to be safety-conscious, reversing into parking spaces or having lids on hot drinks when walking downstairs.
Employees and contractors also need to be able to speak truth to power, and to feel free to speak up when they can see improvements. This means creating a climate of ‘psychological safety’, a term coined by Professor Amy Edmondson of Harvard Business School. Her research includes evidence that companies with a trusting workforce perform better. As she says, “Psychological safety isn’t about being nice. It’s about giving candid feedback, openly admitting mistakes, and learning from each other.”
Assumption-free
In your organisation, there are likely to be highly educated professionals. In my experience there can sometimes be an assumption that because people hold doctorates, they will have a high degree of competency around chemical safety. However, regulations change, and working practices evolve, so in my best secondary school science reference, do not jump to any conclusions regarding policy, protocols and management.
We all know that humans are fallible and can make mistakes, so wherever possible look to remove steps where if something goes wrong harm could result. That is why a hierarchy of control is needed. This involves elimination, substitution, engineering controls, administration controls and PPE.
A systematic approach to working through the stages is required, along with regular documented reviews. Create a positive reporting culture where people can flag and log near misses or accidents, knowing managers will listen and act upon what they are told. If something is identified as risky. act upon it, and ensure there’s a way to guarantee this risk is not found elsewhere. Once again, inform those involved of changes made and that any necessary training happens.
Training & accountability
Training is key, and this has to be systematic and repeated. The importance of safety has to be clearly demonstrated from day one with a standardised induction. Training records must be kept, and with each session a safety angle needs to be incorporated. Personal accountability matters. Reward team members who improve safety performance and recognise their efforts. Involve employees in the safety decision-making process instead of dictating new policies and priorities.
When instituting a new development, explain to affected people why they are being asked to change what they normally do and what success will look like. Ultimately, we need to be as close to zero risk as possible and this means everyone working together.
References:
1. https://ep.totalenergies.com/en/learn-more-about-us/best-innovators-2021/dont-be-dummy-awareness-raising-campaign-hits-home
2. https://hbr.org/2017/05/research-workplace-injuries-are-more-common-when-companies-face-earnings-pressure