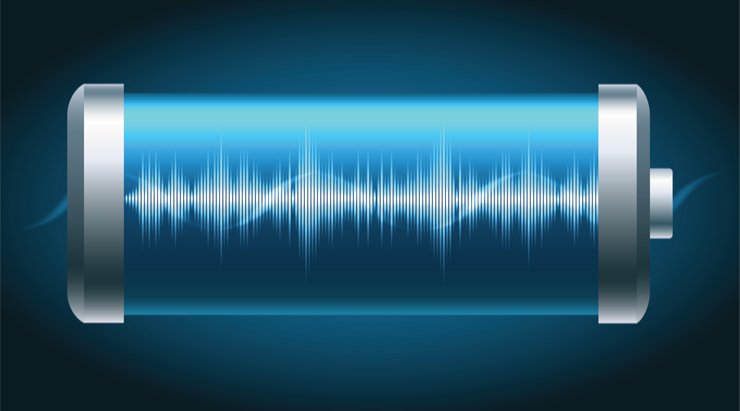
Multiple chemical firms in battery advances
Submitted by:
Andrew Warmington
Umicore has agreed to develop high-performance catholyte materials for solid-state batteries with Japan’s Idemitsu Kosan, combining its expertise in cathode active materials (CAMs) for lithium-ion batteries with that of Idemitsu Kosan in high-purity lithium sulfide. Catholytes combine CAMs and solid electrolytes, enabling solid-state batteries to achieve better performance.
The company has also recently inaugurated its global R&D centre for CAMs next to its R&D centre and production plants in Cheonan, Korea. This comprises a 30,000 m2 complex, with space for growth. Research will focus on next-generation battery materials, including very high-nickel nickel-cobalt-manganese oxide (NMC), low-cobalt NMC, manganese-rich chemistries as well as solid-state battery materials technology.
Separately, Umicore has signed a long-term strategic supply agreement for electric vehicle (EV) cathode materials with Automotive Cells Company (ACC), which is jointly owned by Stellantis, Mercedes-Benz and TotalEnergies. Under this, it will supply next-generation high nickel materials from its site in Nysa, Poland, to ACC’s planned gigfactories in France, Germny and Italy.
The long-term agreement will start with an off-take commitment of 13 GWh/year to a major platform of a European car manufacturer, with the first commercial volumes expected in early 2024. Umicore and ACC see potential to increase this to at least 46 GWh/year by 2030, equivalent to powering at least 500,000 EVs/year.
Meanwhile, BASF Shanshan Battery Materials, BASF’s 51-49 joint venture in China, has announced plans to add capacity for CAMs to 100,000 tonnes/year at sites in Changsha, Hunan province, and Shuizuishan in Ningxia province. This is being done to address booming demand in the electric vehicle.
Due to start up in Q4, the new production lines are designed with high flexibility to produce high-nickel and ultra-high-nickel NCM for polycrystalline and single crystalline products, as well as manganese-rich NCM products. They also feature energy recovery technologies, including off-gas, waste heat and oxygen recycling, a first in the industry.
BASF will also build a commercial-scale battery plant for the recycling of black mass at its CAM hub in Schwarzheide, eastern Germany, where many EV car manufacturers and cell producers are located. Start-up is planned for early 2024. Black mass production is the first step in the recycling process and is based on mechanical treatment of the batteries, yielding a high amount of CAM metals.
Further upstream, Albemarle has inaugurated La Negra III/IV, its third chemical conversion plant, near Antofagasta in Chile. The firm said that this $500 million investment will help to double lithium production and reduce freshwater consumption by up to 30% per tonne of production. It includes a $100 million thermal evaporator to recover water from the mother liquor and recycle it into technical- and battery-grade lithium carbonate.
Nippon Shokubai and Arkema are establishing a joint venture for the construction of an industrial plant for lithium bis(fluorosulfonyl)imide (LiFSI) ultrapure electrolyte salts at Arkema’s Pierre-Bénite site in France by 2026. This will combine Arkema’s fluorochemicals expertise with Nippon Shokubai’s in industrial-scale production of high-purity LiFSI.
Sasol Chemicals and Lotte Chemical have agreed to conduct a pre-feasibility study of a joint project for a plant to produce battery-grade electrolyte solvents at one of the former’s sites in the US or Germany. These help to power Li-ion batteries by allowing lithium ions to travel more easily between anode and cathode.
Finally, Livent has formed an R&D collaboration agreement on lithium metal technology for high-performance battery cells with Munich-based Lilium, which has itself developed the first all-electric vertical take-off and landing jet. Lilium COO Yves Yemsi called this “a milestone in Lilium’s commitment to revolutionise regional air travel”.