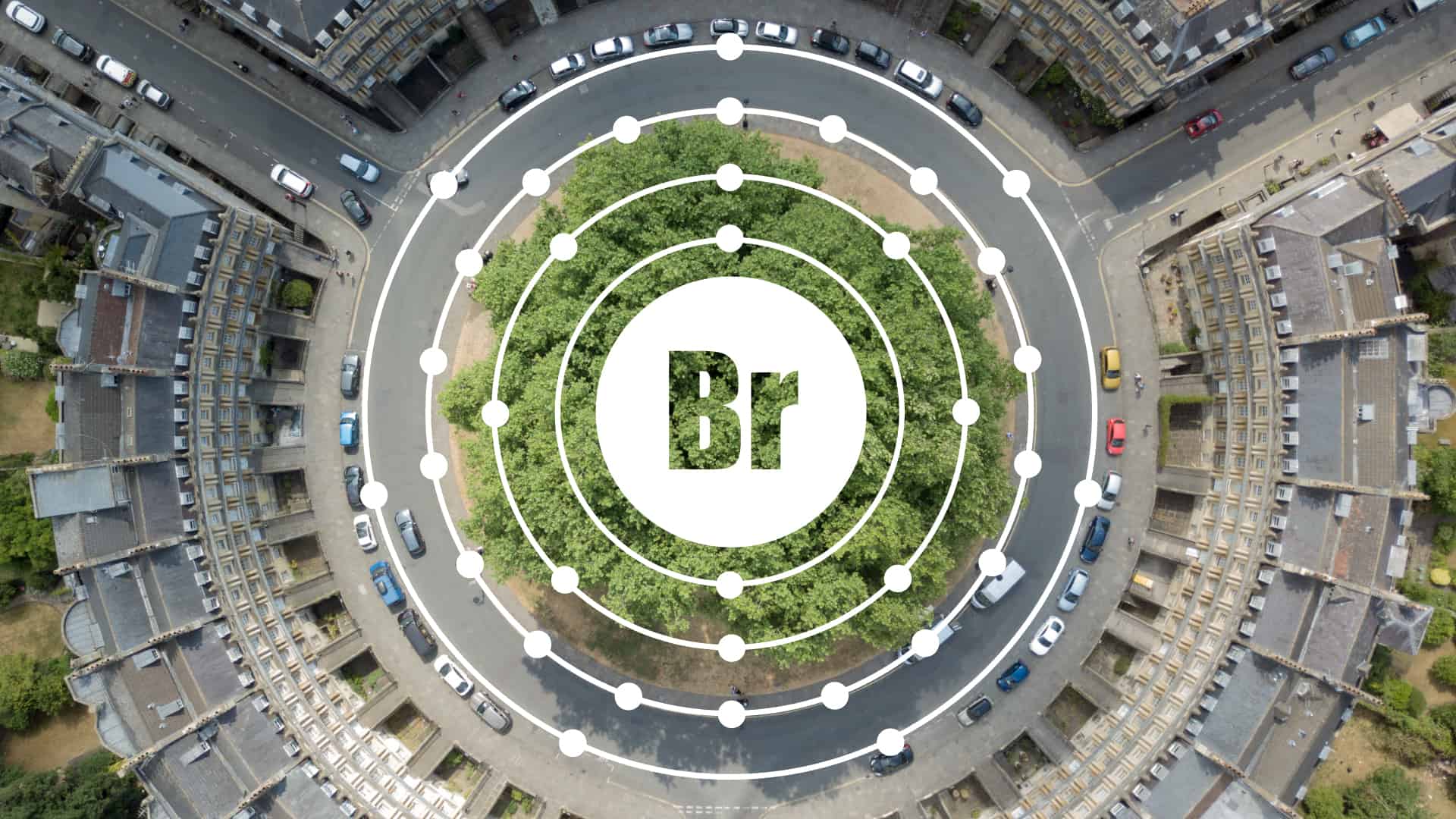
Addressing the circular economy challenge: A perspective on BFRs
Submitted by:
Andrew Warmington
Dr Kevin Bradley, secretary general of the International Bromine Council, takes a look at how brominated flame retardant manufacturers and their associations are addressing the challenges arising from public policy and new business models driving the Circular Economy
In recent years, the challenges of meeting the climate goals set in the 2015 Paris Agreement, coupled with increasing resource use, are challenging policymakers and business leaders to reconfigure production, consumption and resource management within economies, value chains and businesses. The Circular Economy is seen as the approach needed to shift businesses and economies onto a more sustainable energy and resource use path.
According to the Ellen McArthur Foundation, the leading global think tank promoting the concept, the Circular Economy is “based on the principles of designing out waste and pollution, keeping products and materials in use, and regenerating natural systems”. The World Economic Forum and the World Business Council for Sustainable Development have both endorsed it, while many major brands, sectors and other businesses are adjusting their business models and operations to implement the principles.
In the public policy sphere, the EU has taken a global lead in promoting the adoption of Circular Economy models and adjusting its product and resources policies and legislative instruments to increase circularity at the macroeconomic level. This shift is given further impetus by the accelerating renewable and e-mobility trend and also the impact of Covid-19, which is leading to a major review of supply chain dependencies on energy and raw materials.
Bromine industry
The bromine industry, as part of the chemical industry, has substantial innovative capacity. This is a key enabler in the development of ways to accelerate the transition to a circular economy and contribute to meeting the goals of the European Green Deal, the Paris agreement and the UN 2030 Sustainable Development Goals.
In the EU, the International Bromine Council (BSEF) supports CEFIC’s view that guiding principles are needed for the development of a Circular Economy.1 These include:
* Developing a sustainable business case in which economic, societal and environmental aspects are balanced, while maintaining the competitiveness of the European industry
* Increasing the share of circular feedstock, through reuse of materials, using more durable materials, resource recovery and mechanical, dissolution and chemical recycling technologies
* Building on and driving scientific and technological innovations, to better use resources as well as ensure effective and efficient end of life reuse, recycling or other sustainable end of life solutions
* Ensuring a life-cycle approach to effectively ensure the reduction of chemical exposure and emissions
* Taking a collective value chain approach over the lifecycle of materials and products to enhance circularity
* Recognising and reinforcing a risk-based approach to end-of-life treatment of materials containing hazardous substances
BSEF endorsed these principles publicly in its position paper on the EU Circular Economy published in June 2020.2 It also provided its views on a number of the issues and priority actions outlined in the European Commission’s Action Plan.
Additionally, BSEF and its member companies are active in the Chemicals Recycling Coalition, a platform encompassing 39 organisations representing plastics producers, converters, users and recyclers, which is coordinated by CEFIC and Plastics Europe. The coalition is working to develop a clear understanding of what chemical recycling is and to promote its role in helping improve plastics circularity.
Finally, BSEF has developed its own programme to address practical challenges and issues, as well as perceptions, around the use and end-of-life treatment of brominated flame retardants (BFRs) in technical plastics. This programme is designed to generate facts about and understanding of how end-of-life BFRs are used and managed in different applications. It is also being used to generate and support projects to address issues and technical challenges around recycling of BFR-containing plastics.
Bromine & the Circular Economy
Bromine-based technologies already contribute to sustainability and circularity. Bromine offers solutions to a wide range of environmental, social and economic needs, including water treatment, reducing mercury emissions, fire safety, energy storage and generation, pharmaceutical production and enhanced quality rubber.
With respect to BFRs, their use in components and products prevents a major safety and environmental hazard, namely fire. This not only means a contribution to saving lives and preventing injuries, but also property damage.
BFRs are mainly used in plastic polymers and resins. Plastics use and recycling is very much in the spotlight, with substantial pressure on the materials from policymakers and stakeholders who perceive the plastics waste problem as a global sustainability threat. At present, end-of-life plastics products containing BFRs can undergo several waste management treatment options, depending on the amount and composition of the plastics waste stream, as well as on local conditions.
Plastics with BFRs have excellent stability during recycling, which allows the recyclates to meet the same levels of fire safety as virgin material and maintains the value originally provided by FRs in the material.3 Where BFRs are used reactively, such as in the fabrication of FR printed circuit boards, the treatment is driven by the desire to recover valuable precious metals and other metals.4 In such treatment processes (e.g. metal smelters), the resin base of the circuit boards is consumed as energy.
Where BFRs have been used additively – added to the polymer mix – the recycling of end-of-life plastics depends on the management of the products where these are used. For end-of-life vehicles to electrical and electronic products (WEEE), mechanical recycling is used to recover different technical plastics for reuse in new plastic parts and components.
However, four BFR substances are restricted under REACH and RoHS or listed as persistent organic pollutants (POPs) under the Stockholm Convention. POPs are no longer allowed in new products, but are still present at very low concentrations in waste streams.
In the EU, the WEEE Directive (EU 2012/19/EC) requires the segregation and separate treatment of BFR-containing plastics to ensure that restricted substances are removed from the material stream and destroyed or irreversibly transformed. The WEEE CEN Standards provide the basis for recyclers to achieve this and ensure that plastics being used again do not contain legacy BFRs.4
When recycling is not possible for technical reasons, there is a range of waste management options, including advanced solid waste incineration and feedstock for cement kiln. Chemical recycling technologies like dissolution and pyrolysis are also emerging which will lead to the recovery of plastic resins and their reuse in new plastics products.
Are BFRs hindering recycling?
Recycling BFR-containing plastics is perceived as problematic due to presence of legacy POP BFRs. Some stakeholders perceive them as hindering the yield from plastics recycling. BSEF commissioned the consultancy SOFIES to undertake a study on BFR-containing plastics and WEEE recycling in 2020.
The results reveal that BFR additives or BFR-containing plastics are not, the substantive factor when it comes to plastics yield from end of life WEEE plastics recycling. Key findings include the following: In total, 2.6 million tonnes/year of WEEE plastics are generated, mainly PP (20% of the total), ABS (19%), (HI)PS (18%) and PC/PC-ABS (7%). Brominated plastics represent about 9% of the total, mainly ABS (4%), epoxy (3%) and HIPS (1%). The remaining 27% includes other engineering polymers, such as PA 6, PA 6,6, POM, PBT and PMMA.
Secondly, WEEE plastics contain significant loads of additives, whether fillers, flame retardants, plasticisers or others, and as such must be sorted out prior to recycling. On average, 55% of WEEE plastics entering recycling facilities will actually be turned into regranulates.
This yield is mainly influenced by the composition of the plastics, particularly the share of target polymers (PP, PE, ABS, PS and eventually PC-ABS) as well as their densimetric profile. The remaining 45% cannot be sorted using conventional sorting technologies and/or are unsuitable for recycling, due to their detrimental impacts on quality or lack of demand.
The levels of legacy BFRs in WEEE plastics, primarily the PBDEs, have decreased significantly over the last few years, demonstrating the positive effect of regulatory restrictions to phase out these legacy substances. PBDE levels can be expected to tail away to below measurable levels in the coming years and this trend is already evident today.
Finally, 98% of BFR plastics collected can currently be separated and disposed of through official WEEE recycling channels. The report and its recommendations are now being considered with the recycling industry and being shared widely with stakeholders including policy makers and regulators.
Supporting the Circular Economy
As part of its global Circular Economy Action Plan, BSEF and its member companies are engaged in several projects to improve end of life recycling of materials containing BFRs. For instance, BSEF, the North American Flame Retardant Alliance, NAFRA, and its member companies, are supporting a new approach to sorting and separating legacy BFRs from non-restricted BFRs using novel blockchain technology.
The pilot project will involve a chemical-based hidden ‘barcode’ system pioneered by Security Matters, alongside a unique ‘reader’ to identify these codes. These will enable a blockchain record to be developed to store and protect ownership data. The technology will be used to differentiate current and new BFR technologies from legacy BFR chemistry.
The bromine industry, along with its value chain, is also innovating the way it helps manage materials with legacy chemicals. One example of this is the EU LIFE co-funded Polystyrene Loop Project, designed to provide a large scale demonstration plant using the CreaSolv dissolution process. The project involves the construction of a large-scale demonstration plant that can handle 3,000 tonnes/year of PS waste adjacent to ICL-IP’s Terneuzen plant in the Netherlands. This is scheduled to start operations in 2021.
This technology, combined with the high-temperature incineration of HBCDD, which is a POP under the Stockholm Convention, and a bromine recovery unit. This will ensure the recycling of HBCDD-containing PS foam waste into manufacturing-grade PS, full and safe destruction of HBCDD and the recovery of the bromine present in it.
Concluding remarks
The Circular Economy is a journey, not a destination. It will take time, investment, innovation and sound policies to move towards economies that rely more on reusable, repairable and recyclable materials and products. The bromine industry is committed to working closely with policymakers, regulatory authorities, its value chains and other stakeholders to encourage further sustainable end-of-life solutions across the different applications of bromine. Some solutions are easily or more readily available and achievable. Others will take time and require both innovation as well as pragmatism in terms of what is realistically feasible.
Contact:
Nuno Bacharel
Communications Manager
BSEF
+32 2 436 96 01
www.bsef.org
References:
1. CEFIC Views on Circular Economy 2.0: Towards a Carbon-Smart Circular Future
2. https://www.bsef.com/wp-content/uploads/2020/06/BSEF-Position-Paper-Circular-Economy-Action-Plan-June-2020-short-version1.pdf
3. https://www.bsef.com/bromine-the-circular-economy/
4. Article 8.5 of the WEEE Directive 2012/19/EU requires the establishment of standards for the collection, treatment and re-use of waste electrical and electronic equipment. These standards are published by CEN as a series – 50625. S.R.CL/TS 50625-3-1:2015 addresses inter alia treatment of bromine containing plastics