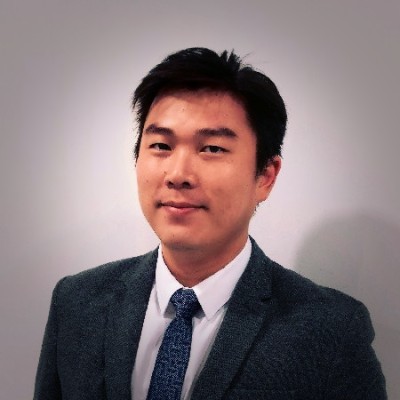
Cleaning up thermal processes in the chemicals sector for a sustainable future
Submitted by:
Andrew Warmington
Patrick Ho, market development manager – chemicals at Gestra, looks at the advantages of finding the right energy partner
With COP27 behind us, the climate focus is on industrial companies and their processes. With the industrial sector responsible for using more than half the world’s delivered energy – particularly through heating processes, which account for up two-thirds of this total – there is an imperative to act. For example, in the UK according to BEIS, industrials and manufacturing were responsible for 16% of overall energy consumption in 2022.
It is no secret that the chemicals industry is heavily dependent on high-heat processes. But it is still early days when it comes to decarbonising these processes. Although making the chemicals industry more sustainable will be neither cheap nor simple, the world has no alternative and we must take urgent action.
The global situation is precarious. Although 34% of the world’s largest companies have committed to a Net Zero target, a recent report from Accenture showed that 93% will have to double their rate of emissions reduction if they are to achieve their goals by 2030. To make matters worse, only 10% of reaction and separation processes in chemical manufacturing can be considered sustainable, leaving a daunting hurdle for the industry.
Reports like this, although shocking, must give the chemicals industry fresh impetus to decarbonise. Genuine and efficient progress towards sustainability in chemical processes can only be achieved if companies consider a variety of different measures, including the electrification of steam production and developing a long-term strategy.
Efficiency as the new normal
Sustainability leaders face a variety of complex options here, which can make it difficult to understand how to build sustainability momentum. Solutions include condensate recovery systems, which boost energy efficiency, or insulating pipes and valves to reduce the heat loss during distribution.
This is where external expertise will prove crucial in helping design, implement and deploy a more sustainable thermal operation that is tailored to each chemical plant. A critical factor in beginning a decarbonisation journey is ensuring that sustainability and energy efficiency efforts are working hand in hand – reducing energy consumption must be part of a wider process of decarbonisation.
Making data count
Striving for efficiency in this way will provide chemicals companies with a full view of their operations and processes, but it is hard to do this without data. Integrating measurable systems makes it easier to spot performance issues in real time, as opposed to discovering issues during a typical biannual inspection. Data is crucial in obtaining this expanded viewpoint, including information from all areas of thermal energy systems, and in developing actionable reports.
With such reports at their disposal, companies will be able to better discern their standing point in energy efficiency and drive the necessary action for true sustainability. Putting an organisation’s path towards decarbonisation into numbers is half the battle.
However, access to data pushes this information further, helping stakeholders in the boardroom understand that their investments are well placed, as well as allowing site managers a more detailed understanding of their system’s performance.
Taking action
Increasing efficiency is a single part of a broader process, and chemicals companies should not postpone the wider decarbonisation efforts until after maximum energy efficiency has been reached. Luckily for these companies and our efforts to tackle climate change more broadly, technology to help decarbonise industrial heating is becoming available.
Be it making steam heating more sustainable by installing new electric boilers or retrofitting existing ones, there are growing numbers of flexible approaches to renewable energy use and storage. Choosing the right energy partner is therefore essential for organisations that want to take advantage of new technology as soon as it comes to market and to establish the best possible combination to tackle their own situations, challenges and sustainability pathways.
The needs of every chemicals business varies, and each company will require a measured, tailored approach to fit its own infrastructure, energy use and targets – there is no one-size-fits-all approach to decarbonisation in this industry. However, there are huge advantages for organisations that work alongside a trusted partner, such as our engineers at Spirax Sarco, to navigate the road to sustainability, combining their expert knowledge, industry relationships and technological expertise.
Although stakes are high, chemicals sustainability leaders should view this as an opportunity to both transform their businesses and create authentically transformational change for the world. The choices that organisations and industries make during this period will be instrumental in building a more sustainable future, and there is no better way to achieve this than taking concrete steps forward on energy efficiency and carbon elimination.
Contact:
Leigh Griffiths
Digital & Content Marketing Manager
Spirax Sarco