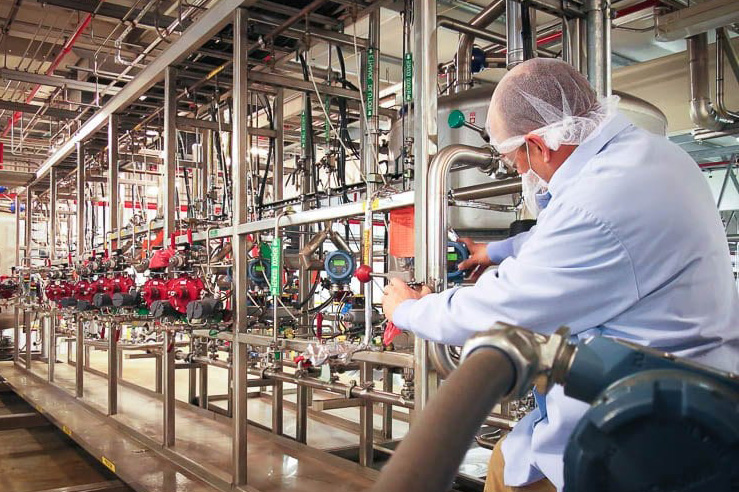
Delayed differentiation skids & product variation efficiency
Submitted by:
Andrew Warmington
Ken Sipes, director of process systems at EPIC Systems, explains the benefits of designing modular process skids for delayed differentiation
Delayed differentiation, also known as late product differentiation (LPD), refers to the practice of postponing changes to a base product until the end of the manufacturing process. This strategy is widely practised by manufacturers of flavours and fragrances, home and personal care products, adhesives, speciality chemicals and others.
The Covid-19 pandemic has also made LPD popular with hand sanitiser manufacturers. Delayed differentiation allows businesses to fulfil growing customer demands for product variations, while also mitigating the overall cost of manufacturing new products. When applied to industrial mixing, LPD creates flexibility by mass-producing the base ingredient(s) and blending additional ingredients downstream.
In recent years, process skid manufacturers have seen an increase in RFQs for these systems. LPD skids, also called inline blending skids, have increasingly been used. By integrating these into their plants, manufacturers are able to create more product variations without having to waste a larger batch that is not needed for smaller orders.
This factor enables manufacturers to have shorter lead times for their products and fill orders faster. For example, they can blend a run of one stock-keeping unit (SKU) for 300 units, quickly wash out the system, then run 1,000 units of a different SKU.
Additionally, LPD keeps overhead expenses lower by providing the production flexibility to make as much, or as little, product as needed at a given time. There are also situations where LPD systems are dedicated to a single product SKU. These usually come about because traditional batch mixing methods would be inefficient, usually due to the infrequency of batch runs, or the ingredient composition.
Delayed differentiation systems come in all shapes and sizes. They can be designed to fit in the most compact areas of a plant or can have a dedicated area of their own. They are also commonly designed for portability, either via fork pockets or even on castors. Some systems have also been installed as permanent fixtures within plants.
Before getting into specific examples of this method in action, it is prudent to understand the definition of inline blending, one of the most common process systems used for LPD. Although inline blending is not rocket science, it requires a level of finesse that can only be had from years of experience. Things such as viscosity, number of ingredients, flow rate/production requirements, and recipes all need to be considered.
Case studies
Recently, EPIC Systems worked with a Fortune 500 industrial chemical company on a project that used enzymes in laundry detergent. These enzymes would break down stains and improve detergent performance but presented an industrial hygiene problem for traditional batch systems by exposing employees to an enzyme with sensitisation issues during the mixing process.
Many engineered controls are required to mitigate the hazard in the handling of these enzymes. Inline blending reduces exposure as the enzymes can be quarantined until right before being added to the filler. Likewise, other hazardous chemicals can be dosed at the last minute through LPD to reduce risk.
In 2019, a Fortune 500 food & beverage company contacted EPIC to assist in the design and build of a portable LPD system for ice cream flavours. The manufacturer was looking to improve its mixing process by reducing washout time and increasing output, while maintaining the product quality of a batch system. This custom-built system pumps a base-neutral ice cream into the system and then injects flavours into the mix.
This system was also designed in a compact and portable manner, including casters, so that it could be moved to different filling lines as needed, eliminating fixed blending equipment at each filler. It has allowed the manufacturer to pilot test and implement a process for inline blending ice cream flavours. As of May, the manufacturer was optimising the system and working towards further rolling out LPD on other lines.
Another project called for a major ingredients module to blend a pre-mix and several other ingredients into a base formula. This base mix was pumped to the second skid, which added dyes, ancillary chemicals and perfumes to manufacture a wide range of end products. The second chemical injection skid was immediately upstream of the filler and both skids featured automated recipe inline mixing controls and variable flow rates.
Further examples
Systems can accommodate numerous ingredients, whether they are to provide SKU variants or are simply part of the recipe. EPIC has engineered systems that could blend several ingredients, as well as ones that blend two or three, such as isopropyl alcohol and water. Inline blending systems also provide flexibility extending beyond LPD.
Following the outbreak of Covid-19, several hand sanitiser manufacturers and co-packers approached EPIC to develop a standard continuous mixing skid that could be quickly installed in strategic locations globally. The process engineering and design teams developed a standard mixing module that meets FDA regulations and allows manufacturers to start producing 10-50+ GPM of WHO-approved hand sanitiser in under eight weeks.
Because of the inherent flexibility of these modular skids, sanitiser manufacturers are able to use them for short-term spikes in demand without compromising long-term return on investment. Because of their modular design, they can be easily relocated, allowing manufacturers to move their dosing system across the plant or across the world, as business needs evolve.
In another example, a major consumer products company asked EPIC to engineer a system that would double its flavour production capacity. The customer needed a system that was able to fit into a small space on a limited budget. EPIC used an industry-standard front-end loading engineering approach to design a system that would meet their needs.
The in-line blending skid uses ingredient trees to mix various products on one small skid, eliminating multiple storage tank requirements. Each ingredient tree has an on/off flow control valve that feeds raw ingredients from the raw materials storage area into the product formula. Flavours are fed from a perfume in-line blending system, allowing for just-in-time mixing and reducing downtime.
The skid also utilises two small tanks. As the product is mixed, one tank fills with the solution. Simultaneously, the other tank is emptied and washed out, prepping for the next product in the queue. This method allows for minimised waste. The 3-5% of product that is recovered during washout is remixed in future runs, allowing for virtually zero waste. The start-up of this system has allowed the customer to inline blend two different product lines, reaching over 25 different SKUs.
Contact
Ken Sipes
Director of Process Systems
EPIC Systems
+1 314 207 4261
www.epicmodularprocess.com/specialty-chemicals