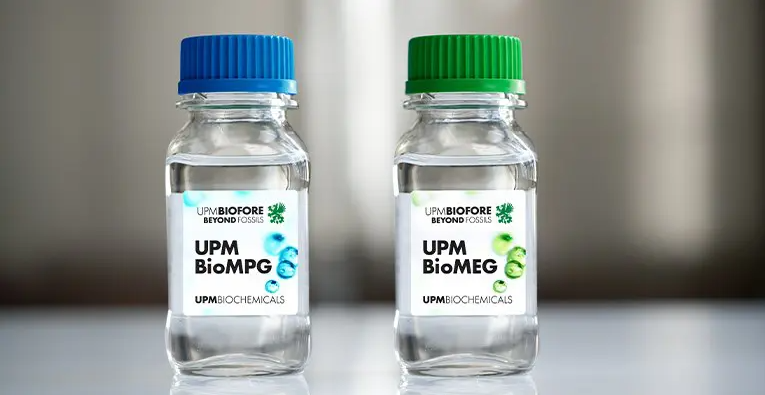
Biochemicals: A future path for textile production?
Submitted by:
Andrew Warmington
The use of renewable carbon from wood to produce biobased products will have a crucial role, argues Martin Ledwon, VP of sustainability at UPM Biorefining
The risks of climate change need little introduction. We are already starting to live with the impacts of a changing climate on the environment, communities, businesses and supply chains. The ambition to limit global warming to 1.5°C is now hanging by a thread, with voices asking even whether keeping within this trajectory is even still feasible. This makes each 0.1°C rise above 1.5°C hugely significant.
With an increasingly narrow window to stabilise climate, it is now incumbent upon major primary industries to take a broader approach to sustainability than solely through decarbonising of energy sources. In addition to championing a truly circular economy, due to its immense responsibility of supplying intermediate products to downstream manufacturers, the chemicals industry needs to curb its high dependency on fossil fuel.
Specifically, this means finding alternative, renewable feedstocks to replace current petroleum-based ones in the production of chemical intermediates. Often referred to as ‘renewable carbon’, the alternative feedstock sources available today are from biomass (typically wood, crops, manure, algae, etc.), from carbon capture or from the recycling of materials already used.
For the purposes of this discussion, we are focusing on wood. Not only is wood one of the most widely available feedstock sources – and, operationally speaking, one of the easiest to directly replace fossil-based sources - its chemical make-up allows for similar or even enhanced performance characteristics to their fossil-based counterparts.
Root of the problem
Only two years ago, textile consumption in Europe ranked fourth with regard to the highest impact on the environment and climate change globally. It was also the fifth highest in terms of raw material use and greenhouse gas emissions.1 If that was not damning enough, approximately 60% of all materials used by the fashion industry and 70% used in homeware textiles are made from fossil-based polymers.1,2
It is evident that industries relying on textiles are facing a major challenge to align themselves with sustainability strategies of other industries. But we need to look back through the textile production value chain, to find the real root of the problem. The global chemical industry is responsible for a vast number of man-made textiles which form a significant part of our modern consumer world - everything from clothing, footwear and bedding to furnishings, carpeting, car interiors and much more.
Producing synthetic fibres or a mix of natural and synthetic materials, the industry generates over $3.5 trillion in revenues annually, representing around 4% of global GDP – roughly equal to the output of Russia, the world’s fourth largest emitting country - and directly employing over 11 million people.3 At the same time, it accounts for 4% of global greenhouse gas emissions, of which the International Energy Agency estimates 75% is from the production of large-volume chemical intermediates, such as ethylene, propylene, benzene, toluene, ammonia and methanol.3,4
However, the chemical industry has so far lagged behind other sectors in transitioning their operations to sustainable models of operation. Until this changes, it is impossible for other sectors reliant on chemical products to be truly sustainable. With almost the entire carbon feedstock used in the chemical system currently from virgin fossil sources, the transition to alternative feedstocks represents an enormous challenge. Finnish company UPM Biochemicals has risen to the challenge and will be the first to produce wood-based biochemicals on a large scale.
Look to the forest
Trees are composed of 20-30% lignin, a complex polymer found in cell walls that gives wood its stiffness and resistance to degradation. This valuable compound can serve as a raw material in the production of biobased chemicals that can be used in the manufacture of man-made fibres, among many other products.
Lignin also offers UV and temperature stability, and even enhances moisture resistance, thus helping to prevent bacterial and fungal attack. It is these properties that make lignin an ideal substitute for various petroleum-based products. It has already found its way into a rapidly growing number of industrial applications such as resins, adhesives, bioplastics and polyurethanes (PURs).
UPM Biochemicals’ new biorefinery in Leuna, Germany, which is due to become operational in 2024, will primarily use beechwood feedstock, from which it will produce 220,000 tonnes/year of biochemical intermediates. The company has ensured that sustainability is built into every part of its value chain. All the wood used is fully traceable and supported by a verified third-party chain of custody, either Forest Stewardship Council- or Programme for the Endorsement of Forest Certification-certified, and sourced from regional forests.
Up to 60%, by far largest part of the wood harvested in Germany, is currently burned as fuel or used for energy generation. Its use in long-life and recyclable products would make the best of the renewable carbon provided by wood and have a bigger impact in mitigating climate change. Using wood wisely in the post-fossil world means reducing the amount of wood used for fuel and energy, and increasing material use to foster a circular economy and work towards zero virgin fossil feedstock. From this fully sustainable source, UPM Biochemicals has developed a new generation of renewable bio-based drop-in glycols. Mono-ethylene glycols (MEGs), PURs and PET are vital ingredients in the production of man-made fibres and materials used in the manufacture of countless types of textiles.
Integration into existing manufacture can be easily implemented because UPM’s bio-glycol, BioPura*, is a molecular like-for-like substitute, enabling a much more sustainably sourced, virgin bio-polyester to be manufactured. Ideally, the biopolyester will be mechanically recycled at the end of life, just as fossil-based polyester should be. If it cannot be, it can be chemically recycled using glycolysis.
This process requires additional MEG to create new recycled polyester and using BioPura here will create a holistic circular economy in the polyester value chain A case in point UPM Biochemicals and South Korea’s Dongsung Chemical recently announced a partnership to accelerate the introduction of renewable, sustainable forest-sourced materials into the Asian market in order to reduce fossil resource consumption.
With the manufacturing of textiles heavily concentrated in Asia – including 88% of all footwear – the collaboration represents a milestone in the development a renewable polyurethane product based on UPM Biochemicals’ biobased MEG. Initially, Dongsung will use this to develop renewable PUR - for which glycol is a primary constituent - for the footwear market. Mid soles – particularly for athletic footwear - are usually manufactured from fossil-based PUR, and while some fossil materials will still be present, the addition of the bio-based PUR will be a major advance in Dongsung’s ambitions to develop more eco-friendly materials. There are already plans to expand the field of application to automotive interior materials and adhesives.
Conclusion
Wood is one of humanity’s most ancient raw materials but it can also take us into the future. Replacing fossil and mineral-based materials with wood-based biochemical ingredients will also lock-in carbon sequestered from the atmosphere for the life of the product. This enables us to radically reduce the carbon footprint of materials and provide better, more sustainable choices to consumers.
References:
1. European Environment Agency: Textiles & the environment: The role of design in Europe’s circular economy, 10 February 2022
2. UN Environment Programme: Fashion's tiny hidden secret, 13 March 2019
3. Systemiq: Planet-positive chemicals: A pathway for the chemical industry to enable a sustainable global economy, September 2022, p9
4. K. Huang et al., Greenhouse gas emission mitigation potential of chemicals produced from biomass, American Chemical Society, 20 October 2021