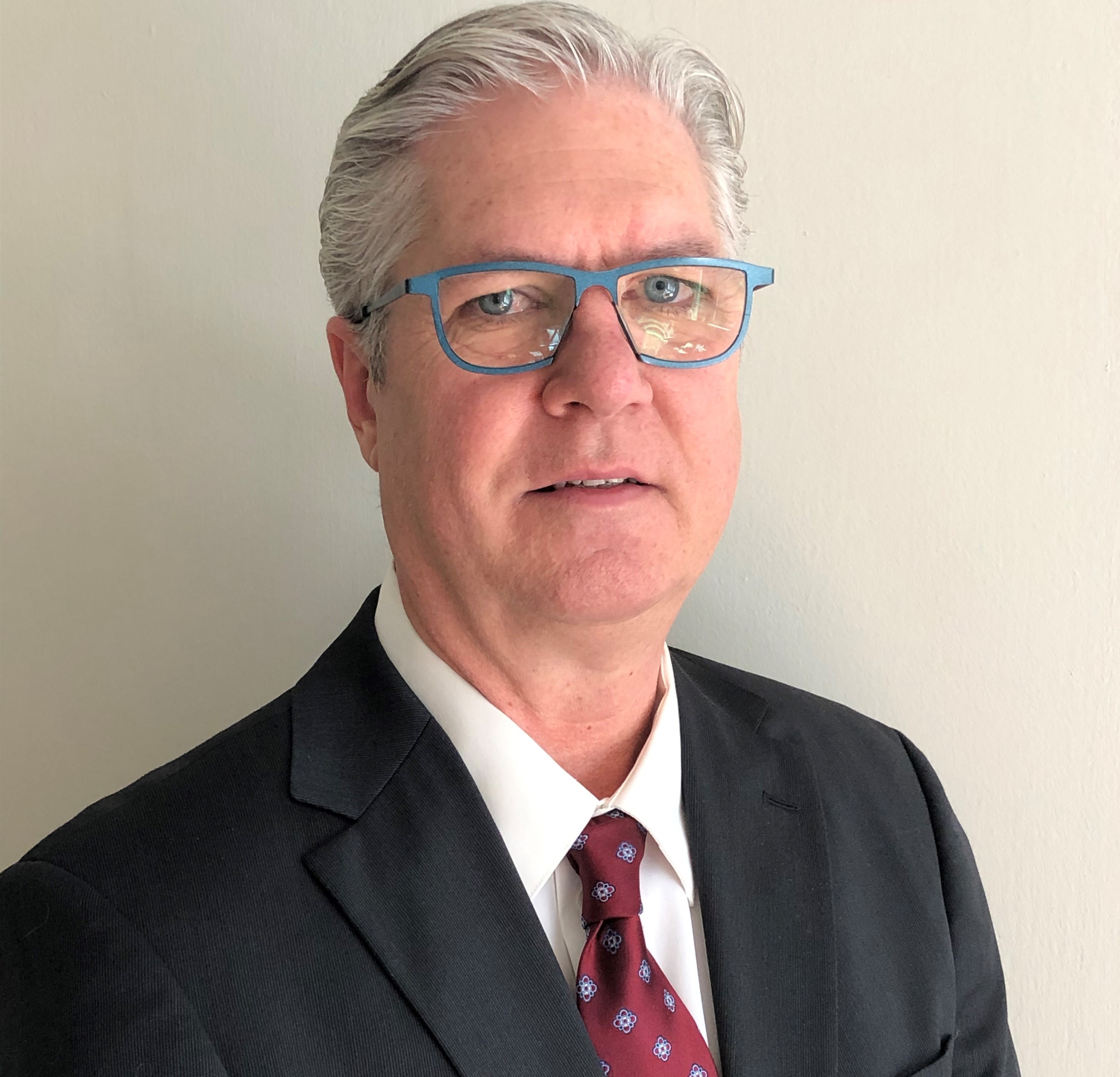
Digital intelligence: The chemical industry’s best counter to rising risk & uncertainty?
Submitted by:
Andrew Warmington
David Dunn, global industry marketing lead for chemicals, at SAP, highlights the need for chemical companies to look at Industry 4.0 practices
Before 2020 spiralled into viral uncertainty, chemical manufacturers had the luxury of embracing digitalisation and Industry 4.0 practices on their own terms. No longer. The fallout from the COVID-19 pandemic has elevated the sense of urgency among chemical manufacturers to infuse their operations and their supply chains with Industry 4.0 capabilities.
Under mounting pressure to capture new efficiencies, add supply chain resiliency, make better-informed decisions and gain agility, chemical companies are accelerating their digitalisation efforts by turning to a variety of Internet of Things (IoT)-connected, data-powered technologies and approaches. By doing so, they are gaining an edge in several key areas, which in turn positions them better not only to weather the volatile near-term business environment but also to thrive in the chemical industry’s ‘new normal’, whatever that ultimately looks like. Those areas include empowered people, intelligent products, intelligent factories and intelligent assets.
Empowered people
The pandemic has provided a powerful reminder that people are as critical to digital transformation as technology. By integrating a greater degree of automation into their operations, a manufacturer reduces risk of manual errors, keeps more workers out of harm’s way and gains more real-time data on which to base decisions.
Digital tools also free workers to focus on the higher-value work that drives competitive differentiation: serving customers and innovating with new business models and revenue streams. Finally, they can help manufacturers to reinforce measures to keep their workforce safe and healthy during a health crisis, giving them the means to conduct health screenings, monitor compliance with social and physical distancing policies, and track employee interactions in the workplace.
Intelligent products
The pandemic has not curbed customers’ appetite for high-performance, customised products. Now more than ever, the focus for chemical manufacturers should be on providing customers not just with products but with positive experiences and outcomes.
With advanced predictive tools fed by data on soil content, climate and other factors, an agrochemicals producer can quickly and intelligently model and develop products like herbicides and fertilisers that are tailored to specific areas and even to specific fields. With a digital platform that accommodates collaboration, a producer can work in tandem with customers to develop customised products jointly. It gains the ability to deliver both mass-produced and individualised products at scale.
Companies that produce chemicals for oilfield operations can do the same, developing digitally assisted formulations using data about the content of the commodity and other field-specific factors. Similar analytic tools can prove valuable for compliance. For example, using a chemical compliance determination engine has enabled Givaudan, a Swiss manufacturer of flavours, fragrances and cosmetic ingredients, to make interactive compliance determinations ten times faster, with a 20-fold increase in mass calculation capacity.
Chemical companies also are building value-added, outcome-oriented services around their digital capabilities, essentially monetising information and creating new services to complement product sales. For example, Syngenta’s AgriEdge farm-management service provides farmers with a full-season view of their operation, with field-level insights, business-level analysis and whole-farm results. They can track inputs, map fields, manage inventories and securely store data from a single digital platform.
Intelligent factories
With an intelligent digital core, to which operational assets as well as the supply and demand chains are connected, a chemical company can optimise production processes to create a more material- and energy-efficient operation, one that is agile enough to respond in real time to unexpected changes in demand and supply.
Predictive quality management tools are enabling Albis, a maker of high-performance polymers, to analyse historical production and process data to identify key quality risks and gain visibility into production line performance. Another company, PeroxyChem, is combining tank sensor data with real-time business data to gain insight into tank inventory levels, enabling it to avoid inventory shortages and to improve storage and transportation planning. Unexpected changes in inventory levels automatically trigger processes such as inspection and maintenance.
The disruption caused by the COVID crisis underscored the importance of supply chain resilience. By integrating supply chain with the digital core, a manufacturer can build a more reliable, resilient and efficient supply network. Using predictive supply chain analytics attached to that core, they can uncover risks, segment and prioritise suppliers, and predict and mitigate bottlenecks.
Intelligent assets
Now more than ever, manufacturers can ill-afford equipment downtime and inefficiency in how they manage their assets. When assets inside the factory, at storage facilities and across other parts of the operation are IoT sensor-equipped, connected to one another and networked with a central digital core, the manufacturer gains the ability to maintain, simulate and optimise overall asset performance while minimising operational disruption across the enterprise. With asset data flowing in real time directly from equipment and systems, through the digital core and across the operation, and with predictive tools to analyse that data, manufacturers can use that increased visibility to avoid outages and generally increase asset value.
In 2019, 50 companies, chiefly asset OEMs, software providers and system integrators, formed the Open Industry 4.0 Alliance. It is working to create a common framework for the digitisation of factories, plants and warehouses, and for collaboration among asset manufacturers and the companies that operate those assets. Aimed at eliminating silos that hamper efficient asset management, the framework is being built on existing standards, like the industrial communication standard OPC UA.
Final thoughts
If digitisation had not been an imperative for chemical companies before 2020, it is now. The benefits of embracing Industry 4.0 capabilities — Accenture estimates that by 2025, digitisation could unlock up to $550 billion of value for the chemical industry — have become too compelling to ignore.
Contact
David Dunn
Global Industry Marketing Lead - Chemicals
www.sap.com