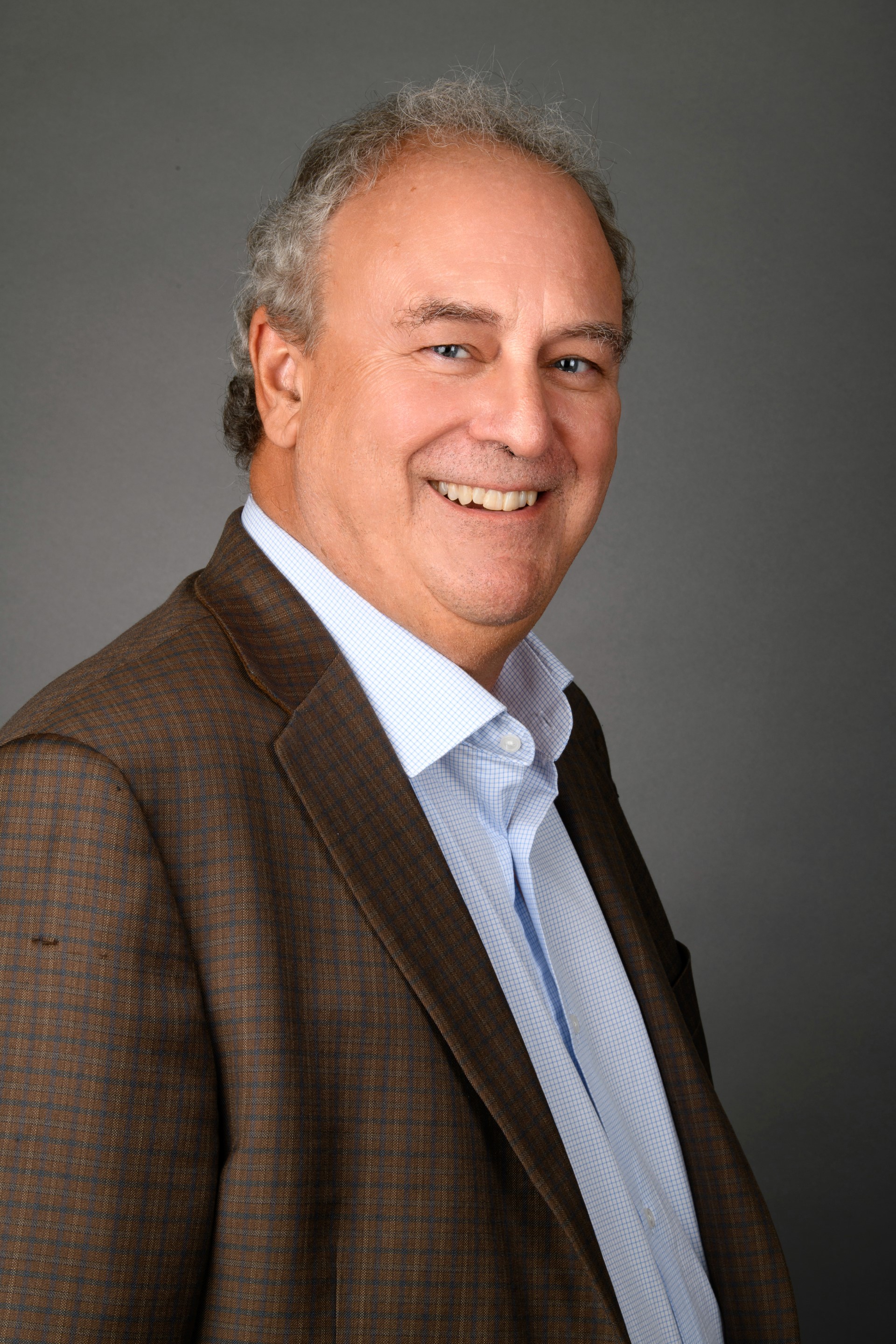
Four strategies to meet chemical industry challenges in 2024
Submitted by:
Andrew Warmington
Stephen Ottley, head of chemicals & energy at SGS Maine Pointe, outlines ways chemical companies can deal with the current uncertainty
The chemical industry is part of every major segment of the US economy and makes up more than 25% of US GPD. When the chemical industry struggles, the economy feels the vibration—and when the economy struggles, the chemical industry reacts. The last 18 months have seen tremendous shifts.
How can chemical companies prepare to weather pressures that depress demand, create supply chain instability and spiral costs out of control? The first step is to recognise the trends. The second, vital step is to prepare now for the next pivot with forecast and demand planning, supplier optionality and strategic procurement, network and footprint optimisation, and greater control and visibility over costs.
Four trends
Both the industrial and manufacturing sectors, major consumers of chemicals and chemical products, had flat or nearly flat growth through 2023. While they may begin to recover in 2024, recovery will be slow. Meanwhile, demand for consumer goods, which sustained the chemical industry through 2023, is beginning to slow down after two years of inflation.
Competition has increased for both raw materials and the technologies to process them. Many companies, including the semiconductor, automobile, and steel, are in direct competition with chemical companies for the same resources. Geopolitical pressures and volatile prices make it difficult for chemical companies to match supply with demand; overstocks and stockouts are common as chemical companies struggle to predict their customers’ needs.
Conflicts throughout the world are making supply chains vulnerable, notably with feedstock and gas supply interruptions in Europe due to war, labour disputes, weather and accidents. In 2023, conflict in the Red Sea caused a 70% drop in container volumes, while labour strikes in France affected the chemical industry supply chain worldwide. In 2021, one ship wedged sideways in the Suez Canal blocked transport for six days.
A riskier supply chain raises the cost of goods sold (COGS) and landed costs (equal to COGS plus after-sale expenses). So many elements go into COGS and landed costs, including hidden costs such as licensing and payment processing fees, and so many variations may occur with each product and customer that chemical companies can have a hard time figuring out how to control and reduce expenses.
Four strategies
To achieve their goals for 2024 and beyond, chemical companies need to better balance supply with demand, strengthen the resilience of their supply chains, optimise operations, and gain visibility into costs. Changes to one part of the supply chain can no longer be made in isolation. Both communications and accountability must extend beyond individual functions if initiatives are to add value across the enterprise. Four key strategies are as follows:
1. Forecast/demand planning: AI-driven systems monitor inventory in real time to optimise levels, reduce stockouts and improve customer satisfaction. Predictive analytics give insight into historical data, market trends and external factors to improve demand forecasting, a better method than relying on historical data alone. Prescriptive analytics help determine the best path to meeting company goals, aligned with KPIs and metrics. Effective sales, inventory and operations planning ensures that every function is on the same page.
2. Supplier optionality and strategic procurement: Part of the procurement function is to de-risk the supply chain by avoiding sole supplier and sole country sourcing. By increasing supplier optionality, companies ensure that, if one source or one transportation route becomes vulnerable, an alternative is available. In addition, strategic procurement continually evaluates raw material, 3PL and other suppliers against company goals. By developing sustainable relationships with key suppliers and developing optional suppliers, a company creates a more resilient supply chain
3. Network & footprint optimisation: Rationalising and optimising asset availability and utilisation, layout, workflow, and footprint design helps to adjust capacity to demand and right-size operations. Simulation models using real-time or near real-time data can reveal those bottlenecks and gaps that create imbalances between productivity and inventory. A capability, capacity and cost assessment identifies areas that are core to the company’s business, those that should be outsourced and those that should be kept in-house because they provide a competitive or financial advantage
4. Visibility and control over costs: Millions of dollars in savings are within reach when companies have true visibility into landed costs by customer and by product. Data analytics, spend cubes and dynamic cost models help create that visibility. A company benefits from standardising spend categories; linking product pricing to its suppliers’ strategy to prevent margin leakage; and addressing issues in invoicing and payment. Market savings are table stakes available to every competitor, but index-based tracking, pricing transparency and visibility over spend provide true and lasting competitive advantage
In one case, a speciality chemical company experienced a steady erosion of EBITDA. Instead of simply lowering spend, the company’s leadership looked for a combination of value creation initiatives that would bring long-term benefit. With upgrades in procurement, logistics and operations, the company was able to gain over $18 million in procurement savings, $4 million in logistics savings, and an 11% improvement in productivity, ensuring that they would be ready when demand increased.
Conclusion
Competition for raw materials, risks to the supply chain, and difficulties in controlling costs are part of doing business in the chemical industry. Short-term solutions leave a company vulnerable with every economic, geopolitical, labour, technology and environmental shift.
A better approach is to develop the tools and structure to strengthen the end-to-end supply chain and its ability to pivot quickly. Strategies that improve forecast and demand planning, supplier optionality and strategic procurement, network and footprint optimisation, and visibility and control over costs give a chemical company the ability to engage in ongoing value creation and growth, whatever challenges lie ahead.
Contact
Stephen Ottley
Senior Managing Director, Head of Chemicals & Energy
SGS Maine Pointe