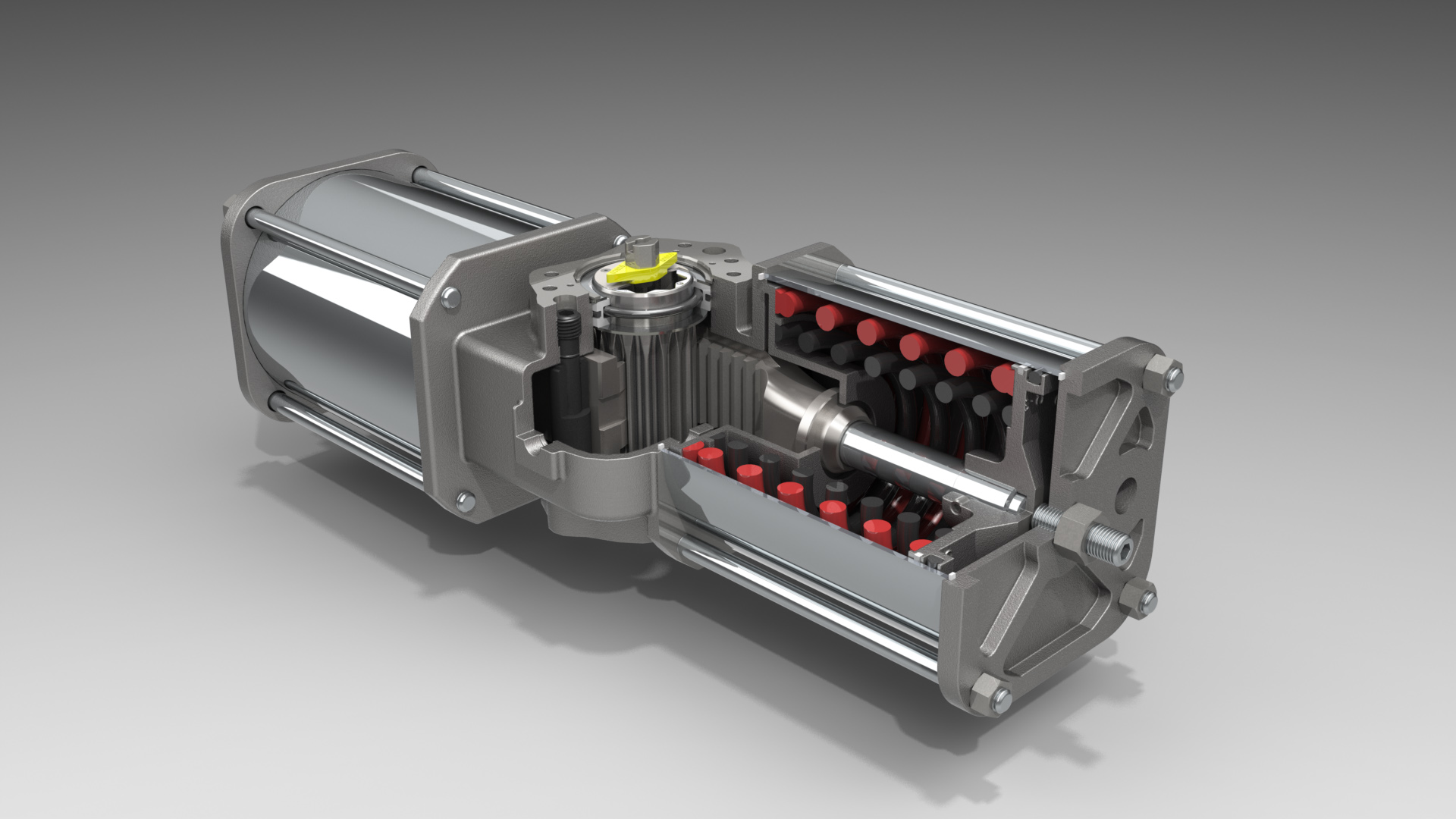
Making actuators last
Submitted by:
Andrew Warmington
Well-designed actuators can offer reliable performance for years with minimal maintenance or repair, says Jeff Elliott
High-speed, high-cycle actuators open, close or throttle valves to regulate, direct or control the flow of gases, liquids, fluidised solids or slurries in chemical manufacturing processes, among others. Many processors have become accustomed to the idea that high cycle actuators have a short lifespan and necessitate regular maintenance to replace parts prone to wear, such as O-rings, springs and cylinders. In some facilities, this task can consume a technician’s entire work schedule.
Many processors are beginning to reassess this expectation, given the high costs for installation and maintenance. A well-designed actuator should be able to provide reliable performance for many years beyond the warranty period. If maintenance or repair is needed, it should be infrequent and simple enough for a single technician to handle, using common tools. For maintenance or repair purposes, the actuator should be easily accessible without the need to remove it from the valve. This is a crucial factor, as valve manufacturers will invalidate warranties if the actuator is detached from its mount.
High demands on actuators
Actuator usage and stress are often linked to the frequency of valve opening and closing cycles. The cycle count often varies based on the environment or application. Some actuators are seldom used, while others operate regularly. High cycle, high-speed valve actuators can fire rapidly and repeatedly many times per hour, non-stop all year.
The core issue lies in the high utilisation and demand placed on the actuator. These come in different styles based on the mechanical action required, such as linear or rotary, but all involve moving parts that experience considerable force, wear and stress. Actuators are also installed in highly corrosive industrial settings. Many designs fail to account for these factors and are poorly engineered, leading to excessive side loading, wear on non-wearing parts and various other issues.
High reliability is another crucial factor that holds significance for Scott Howard of NewGen Products, a specialist in valve automation. Many of his customers are in the aerospace industry, where valves with actuators regulate the flow of cryogenic gases for fuelling and storage operations. For critical applications like these, Howard often recommends a purpose-built actuator.
Although there may be a higher initial cost, these actuators are designed to perform reliably in challenging and harsh environments. Even within this category, however, many are rebuilt every three to four years, Howard says.
Alternative actuators
One exception to this rule, according to Howard, is the actuators built by Texas firm QTRCO. These feature a mechanical design that eliminates common failure points like sliding parts, side load forces and multiple seals. This makes them suited to demanding applications in extreme temperature, corrosive or submerged environments.
QTRCO claims that its actuators address the inherent design limitations of the common ‘lunchbox’ actuator, so called because it is made from a one-piece aluminium extruded body and cylinder that resembles a lunchbox. These are compact, inexpensive and work well, but they are not very reliable and often break in more demanding environments or applications.
QTRCO has designed an actuator with an internal ‘rack and gear’ mechanism as an alternative to its traditional ‘rack and pinion’ design. It is designed with offset cylinders that align the piston axis with the pinion gear pitch circle diameter, eliminating cantilever forces and friction. The company also replaced the sliding blocks, wear pads and bushings with specialised rollers. As a result, the actuator has extremely low internal friction.
In addition, the new design also eliminates one of the primary causes of failure of a lunchbox actuator: the O-rings on the shaft. The action is reversed and the air is forced inward through the end cap. The spring return applies no pressure to the shaft seals, which prevents premature O-ring wear. This configuration also has benefits when valve throttling is required.
Due to the design of the company’s Q Series and because the piston is located close to the end cap, much less air fill volume is required, and the actuator responds much quicker and is easier when throttling. QTRCO took a similar approach as an alternative to Scotch yoke or slotted link actuators. This is a simple, effective and long-used mechanism but the force applied to the piston rod is also applied to the shaft and shaft bushings, resulting in friction and bushing wear.
To resolve these issues, QTRCO designed a patented flat yoke mechanism that can position any rotary control valve requiring up to 500,000-inch lbs (56,000 nm) of torque. This is designed with quad body slots that absorb the mechanism’s side loading forces, leaving the piston rod completely free of bending stresses while allowing termination of the rod at the yoke. Like the Q Series, these F Series actuators also have extremely low internal friction, consume minimal air and can handle the most severe throttling applications.
Frequent replacement
With an actuator specifically designed for reliable and long-lasting performance, processors can save on costs associated with more frequent replacements. In one processing plant Howard visited, the actuator fired twice per minute throughout the entire year, adding up to over one million cycles/year. The plant replaced the actuator annually during planned outages.
According to Howard, replacing an actuator typically requires an entire day for a single technician, often with the help of at least two others. If the actuator is large enough, a crane is required. Considering the potential costs for hourly labor rates and rentals, a plant could save thousands of dollars every time it eliminates the need to replace an actuator.
When preventative maintenance or repair is required, it should be conducted using common tools and without removing the actuator from the valve. With large, metal-seated ball valves, it is critical to mount the actuator with extreme precision. A slight misalignment during mounting can result in severe damage to an expensive valve. The connection is so crucial that most major valve manufacturers will void warranties if the actuator is removed.
In rare cases, like with QTRCO designs, the actuators can be easily maintained without removal from the valve. This enables hassle-free removal and replacement of end caps, cylinders, and O-rings, often without special tools. Safety concerns According to Ross Evans, also of NewGen Products, safety is another concern during preventative maintenance and repair. Large actuators may require two people for lifting and moving.
“Imagine being in a plant environment and climbing six flights of stairs to a catwalk to service an actuator. With that kind of weight, what does it take to get your cranes and rigging in place to safely take off the actuator? You have to remove all the pneumatic airlines, disconnect the electrical, and you need a couple hands. There’s a lot of cost and time and risk involved,” Evans says.
“The alternative is, I can do maintenance on the valve while it is in place,” adds Evans. “I shut down the unit, tag it out, take off the end cap, inspect the cylinder, remove an O-ring, grease it, and put it back in place. In about ten minutes per cylinder, we are back and running.”
The actuator’s design can also contribute to safety concerns. Many Scotch yoke designs feature a lone piston assembly on one side of the unit. Lifting or rigging an unbalanced, single-piston assembly is challenging due to its significant lean on one side.
For high speed, high cycle processing applications, QTRCO recommends sizing up to a two-piston version of its flat yoke design. The two pistons balance the forces on both sides of the shaft, preventing bushing wear.
The design also includes the addition of a weight and force balancing second force module diagonally offset from the first. By balancing the forces, there is less friction and wear and no net force applied to shaft bushings. The balanced weight also makes lifting and handling of the actuators safer and easier, while reducing valve neck stress that can occur in unbalanced scotch yoke actuators.
Another issue is the spring set used in many lunchbox actuators, which are under load and must be controlled safely once the end cap is removed. If the spring becomes jammed and the mechanism that contains the spring fails, the force exerted can be equivalent to a shotgun.
“In one actuator, the end cap corroded and failed. It discharged the spring out of the actuator across the shop,” says Evans. He has personally observed experienced field technicians moving out of the line of the cylinder to remove the end cap on the actuator because of the potential energy contained in the spring.
With QTRCO, the spring is fully captured using a solid stainless-steel rod that goes through the spring retainers and there is a safety collar that locks it into place. Replacing the springs simply requires removing the end cap and replacing the cartridge. Once they capture those springs, it is designed never to come apart again.
Summary
Installing actuators that are built to last and require minimal maintenance or repair not only brings significant benefits, but also proves to be more cost-effective in the long run, even if the initial cost of ownership is higher. When multiple actuators are installed in a plant, the savings can add up. With an actuator specifically designed for reliable and long-lasting performance, processors can reduce costs associated with a labour-intensive manufacturing component that too often requires frequent maintenance, repairs and replacement.
Contact
QTRCO
+1 281 516 0277
https://qtrco.com/