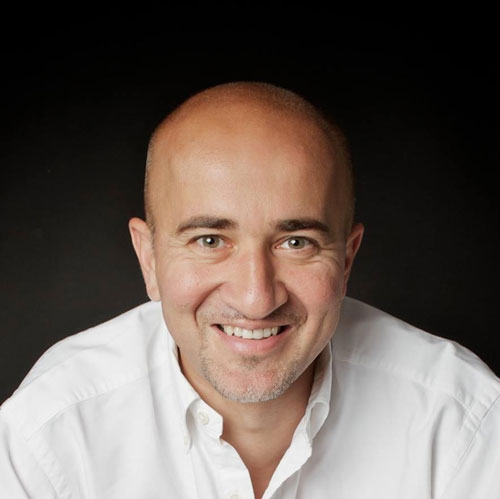
The next age of supply chain scenario planning
Submitted by:
Andrew Warmington
Jim Bralsford, industry and solutions marketing at Kinaxis, addresses how advanced analytic and planning techniques can help the industry in challenging times
The easing of COVID-19-related restrictions and lockdowns did little to move supply chains out of the spotlight. Only recently has China eased its zero-COVID policy that was in place for almost three years, which resulted in a number of manufacturing shutdowns and logistical delays due to labour shortages and reduced capacity. The continuing invasion of Ukraine has led to sanctions on Russia that organisations worldwide have had to navigate around.
In addition, rising energy prices have led to concerns around business viability and created panic among consumers. Lastly, the threat of global recession will likely ease demand from consumers for certain products, leading to impacted profitability.
The speciality chemicals sector has not been immune from evolving supply chain challenges. Deloitte’s survey of 23 of the largest chemical and speciality materials companies discovered that increasingly complex customer demands, such as for customised goods, are placing a strain on organisations as commoditisation and dematerialisation takes hold.
A saturated Western market has led value chains to move to Asia. Supply volumes (68%), on-time shipping (58%), product consistency (51%), price stability (50%) and financial stability of suppliers (44%) are among the top concerns of speciality chemicals industry professionals. While there is no silver bullet that can address all of these issues, supply chain planners can take steps to build potential scenarios across the short, medium and long term with the help of real-time data.
Growing disruption
Supply chain disruption was escalating long before the pandemic materialised. As businesses become much more reliant on a greater scope of global suppliers and manufacturers, scenario-focused supply chain planning has come to the fore as the best (or only) means of having full transparency over what is happening outside an organisation’s own four walls. The pandemic only catalysed this trend away from silos and towards the need to leverage concurrent scenario planning across the supply chain.
Research suggests that wider supply chain skill shortage is expected to leave 2.4 million positions unfilled between 2018 and 2028, with a potential economic impact of $2.5 trillion. Everybody in the industry is in it together, so the need for more advanced scenario-planning systems to provide a single source of truth for more accurate evaluations across the supply chain is more pressing than ever.
A shallow talent pool is creating further issues in the speciality chemicals sector in particular. The industry faces some of the biggest talent shortages because employees usually require specialised skills. Furthermore, there is a lack of new talent coming into the industry. In the UK for example, there are 30,000 more employees aged 40-64 in the industrial sciences sector than those in the 16-40 age group. We need to find ways to turn this around.
Gaining clarity
With businesses needing to ensure resiliency and cost savings from the get-go, scenario planning is coming to the fore. There are two approaches when it comes to scenario planning: known and expected challenges, and completely unknown disruptions.
By working against specific KPIs, businesses can analyse potential scenarios and approach expected challenges with confidence. Combining these options with dashboards and scorecards that clearly articulate the expected outcomes of each choice can enhance decision-making, giving businesses that all-important pivot ability and a clear understanding of the impact of successive changes.
It is a more difficult challenge for the factors that are shrouded in mystery. With so many tweaks and variables needing to be considered, supply chain planners need the ability to eliminate quickly those choices that are not going to meet the KPIs. The faster scenarios can be run, the more options can be attempted, piece-by-piece, to give businesses the best chance of finding a solution that works.
Quickening the pace
The ability to react quickly is a must-have capability to deal with global supply chain disruptions. If a disruption continues to affect the supply chain, organisations are more likely to take a hit on delivery speeds and overall revenue figures. For supply chain planners, the pressure is on to get ahead of problems quickly so as to avoid ripple effects across the rest of the organisation.
In years previous, cost reduction and efficiency optimisation were the priority in supply chain design. The race to chase down the perfect plan, or 100% forecast accuracy, disadvantaged many practitioners as their singular focus on optimisation led to them failing to build enough agility and resilience into their supply chain. It would take hours or even days to calculate a plan, by which point the ‘ship has already sailed’ when fast-moving disruptions like COVID occurred.
However, this is largely no longer the case; businesses in the speciality chemicals sector (as elsewhere) must focus on improving efficiency, speed and agility as global supply chains increase in complexity. The sector is now turning to technology to ensure the right balance is struck between agility and optimisation – and advanced analytic and planning techniques are offering a compelling way forward.
Leveraging data
The way that data is leveraged is key to bringing in the next age of supply chain scenario planning. Crucially, it gives organisations the end-to-end visibility of operations associated with third-party suppliers, partners and the trends associated with customers. Data insights are crucial in giving planners the visibility and transparency needed to run effective scenarios. However, access to transparent data is just the first step.
The next step is adding a layer of quality to enable improved supply chain decisions. Without consistent, correct, up-to-date data, the outcome of a scenario will be fundamentally wrong. An effective scenario must be founded on a solid understanding of exposure, inventory and the true nature of demand – whether it is driven by panic or longer-term trends, for example.
Artificial intelligence (AI) and machine learning (ML) are helping to drive data-driven scenario planning. With talent shortages and the volume of data in such systems growing exponentially, these systems provide insights that humans may not have had the ability or time to discover themselves. AI, in particular, can efficiently process data and pass on key insights to human supply chain planners, allowing them to review the insights and formulate the strongest possible ‘what-if’ scenarios.
Conclusion
The speciality chemicals sector, like many others, will understandably be concerned about the next unpredictable global supply chain disruption. However, they can gain control, and improve agility and resilience, with the help of data-driven, technology-enabled scenario planning. Data from the pandemic already tells us that businesses who made use of supply chain management and operation planning software outperformed the industry average by 2.5 times on average. With AI and ML also coming into play, data insights will become increasingly sophisticated, enabling organisations to better deal with disruption in future.
Contact:
Kinaxis
www.kinaxis.com