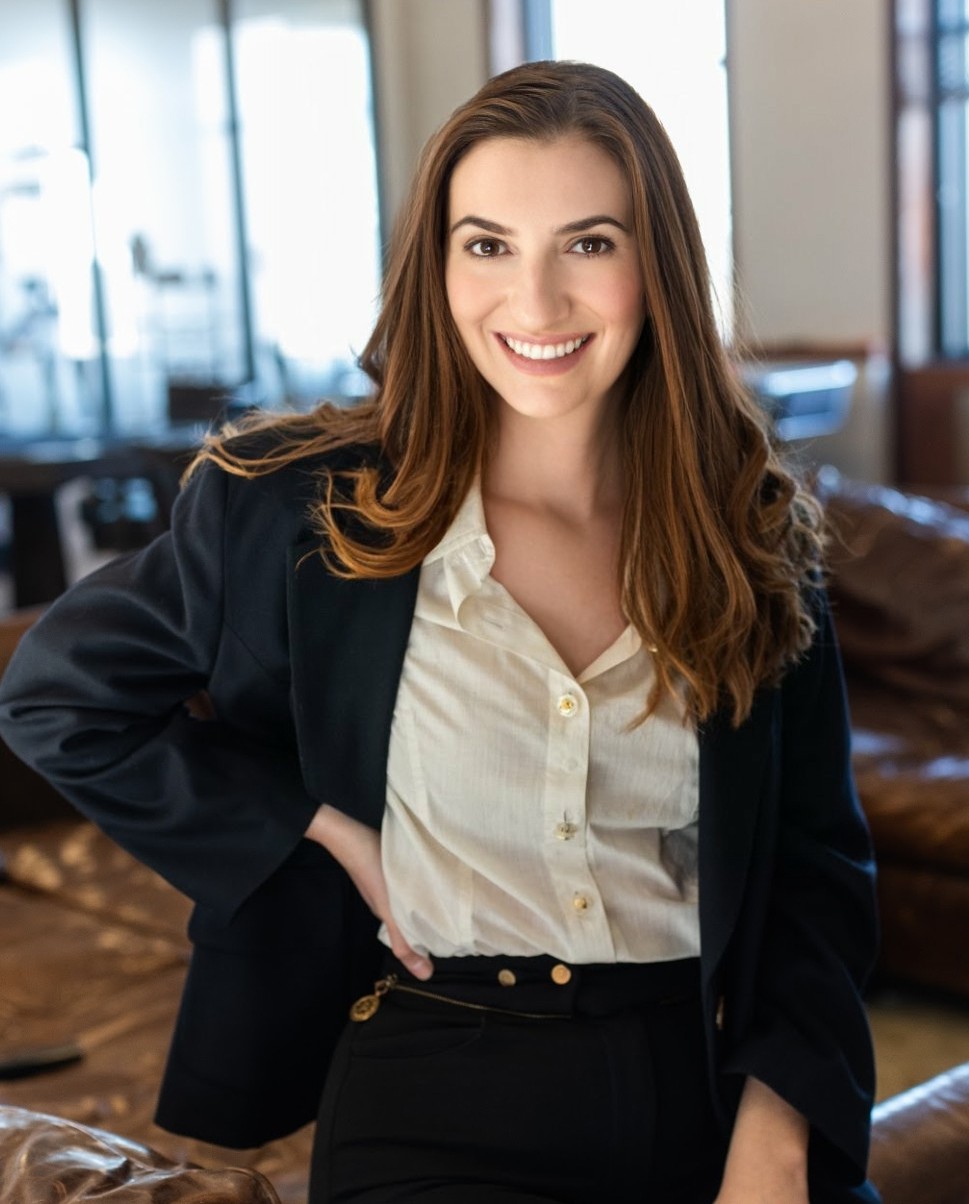
Six ways preventive maintenance improves chemical processing
Submitted by:
Andrew Warmington
Emily Newton, editor of Revolutionized Magazine, looks at how chemical processing plants can improve their performance by anticipating rather than reacting to maintenance issues
An ongoing trend in the chemicals industry is decision-makers at processing plant transitioning to preventive maintenance rather than reacting once problems with company equipment become apparent. This article highlights six specific reasons why this is a reliable way to optimise chemical manufacturing.
Consistently high quality levels
Preventive maintenance contributes to ongoing high quality levels at chemical processing plants because it makes people more aware of potential problems. When issues go unaddressed for too long, there is a higher chance of them eventually affecting quality and perhaps even causing recalls.
Plant managers can even connect preventive maintenance to lean manufacturing processes that reduce waste.1 For example, lost productivity due to wasted time can happen when someone does not have immediate access to equipment being worked on. Users can note usage times in logbooks, confirming when preventive maintenance should occur. That makes it easier to plan workloads while maintaining the excellent quality customers expect.
Enhanced facility safety
Chemical processing is like all other industries in that it has risks to minimise. Safety procedures and employee training are two factors that can keep people safer and avoid regulatory scrutiny.
However, preventive maintenance can play a similar role in boosting safety — as long as the responsible parties periodically review and update maintenance plans as appropriate. It is not enough to follow one preventive maintenance plan and expect it to remain effective for years. Procedures will change if plants start making new products or invest in more equipment, for example.
A joint statement from the Chemical Safety Board and the Chlorine Institute in the US advised: “Preventive maintenance is neither an option nor a luxury — it is one of the most important elements of safety in the chemical sector.”2 The document also mentioned several incidents where inadequate preventive maintenance was a factor in issues faced by the respective plants, including one that could cause steel equipment to fail.
“To be effective, facility owners, operators and employees must put time and resources into developing and executing preventive maintenance programs,” the statement continued. “Yet merely sticking to a plan, however necessary, is insufficient in light of the changing nature of the industry and the workplace.”
Solving operational issues
It becomes challenging to optimise chemical manufacturing when the primary approach to maintenance involves reacting to identified problems. Adopting a maintenance plant that aims to prevent issues often creates a richer history of data that professionals can use to pinpoint issues. For example, refractory lining wear is a common issue with industrial boilers and furnaces.3
Data collection is an excellent starting point that helps repair technicians identify failures. It can also address other maintenance issues that affect the chemical processing sector.
In one example, a chemical plant experienced three emergency shutdowns in as many months due to the failure of an essential piece of equipment. Making matters worse, the abrupt stoppage caused solids to build up in the machine’s pipes, slowing the start-up procedure.
The company addressed the issue by deploying enhanced data monitoring and changing its preventive maintenance plan. It also revised emergency shutdown procedures, which caused a 90% reduction in the subsequent start-up times.4
Increased ongoing accountability for maintenance
Preventive maintenance strategies can also help a plant’s maintenance professionals have a greater sense of ownership about the tasks they perform. One reason is that standardising the processes associated with upkeep makes it easier to ensure equipment performs as expected.
It is not always enough to have a task carried out at the correct interval. Asking everyone to follow the same processes helps improve overall outcomes. It also increases the knowledge transfer among a maintenance team.
One person conducted an informal experiment by asking the top four mechanics in a department to describe their actions when performing preventive maintenance on a particular machine. All had different responses. In addition, each was engaged in a specific step that the others did not know was required.
This inconsistency was not due to a lack of experience in any of them. Each had been at the facility for at least seven years. However, if a manufacturer stipulates how to carry out preventive maintenance and not just when, it would greatly cut down on the possible variability that could compromise a maintenance programme’s success.
Improved maintenance investments
Switching to a maintenance plan that prevents problems can also help plant executives to see larger short- and long-term payoffs as they optimise manufacturing. For example, when companies focus on reactive maintenance, they may face higher repair costs for specially-ordered parts and urgent assessments from technicians.
Additionally, reactive maintenance programmes typically only target the problem at hand. That could mean other issues exist that will soon cause headaches too, but the signs are not obvious yet. In contrast, preventive maintenance involves thorough examinations that frequently catch most problems before they become catastrophic.
Problem prevention also makes it easier for company leaders to predict how much they will spend on maintenance and budget accordingly. Unexpected costs almost always accompany surprise equipment failures. Chemical processors can avoid those by treating maintenance as an ongoing expense that should prevent higher costs down the line.
Some companies even have planned shutdowns for maintenance. Doing that causes a short-term profit loss due to the lack of activity but boosts the bottom line overall by preventing later outages.
Greater flexibility when planning maintenance
Although preventive maintenance involves periodic equipment checks, it does not necessarily mean people must examine them at precise intervals. There are two general scheduling methods in upkeep.
The first involves following a fixed schedule, which means that the upkeep happens at a set time. A major advantage of this approach is that the previous maintenance date becomes a guideline to plan future needs.
A fixed schedule is also useful when data shows a piece of equipment had an above-average rate of problems. Checking the machine at regular intervals catches abnormalities early.
However, some chemical processing companies follow floating schedules for preventive maintenance. They still require checking equipment regularly, but there is a bit more freedom in the timing. For example, a floating plan with a usage-based trigger necessitates tracking the number of service hours and setting maintenance dates accordingly.
Some companies also use floating schedules to check machines based on priority levels. For example, a piece of equipment critical to all of a chemical plant’s operations may get scheduled upkeep more often than a nonessential one. This allows facility managers to allocate their resources as necessary and switch production to rely on a machine that does not require maintenance yet.
Conclusion
Preventive maintenance makes good business sense. The chemical processing sector is certainly not the only industry that often prioritises preventive maintenance. However, the six advantages discussed here highlight why the approach can optimise chemical processing by improving quality, enhancing consistently and avoiding unexpected expenses.
Contact:
Emily Newton
Editor-in-Chief
Revolutionized
www.revolutionized.com
References:
1. www.labmanager.com/business-managers-apply-lean-tools-to-chemical-process-development-1609
2. www.safetyandhealthmagazine.com/articles/16955-csb-chlorine-institute-call-for-regular-assessment-of-preventive-maintenance-plans
3. https://mcneilusa.com/blog/replacing-refractory-materials
4. www.mckinsey.com/business-function/operations/our-insights/predictive-maintenance-the-wrong-solution-to-the-right-problem-in-chemicals