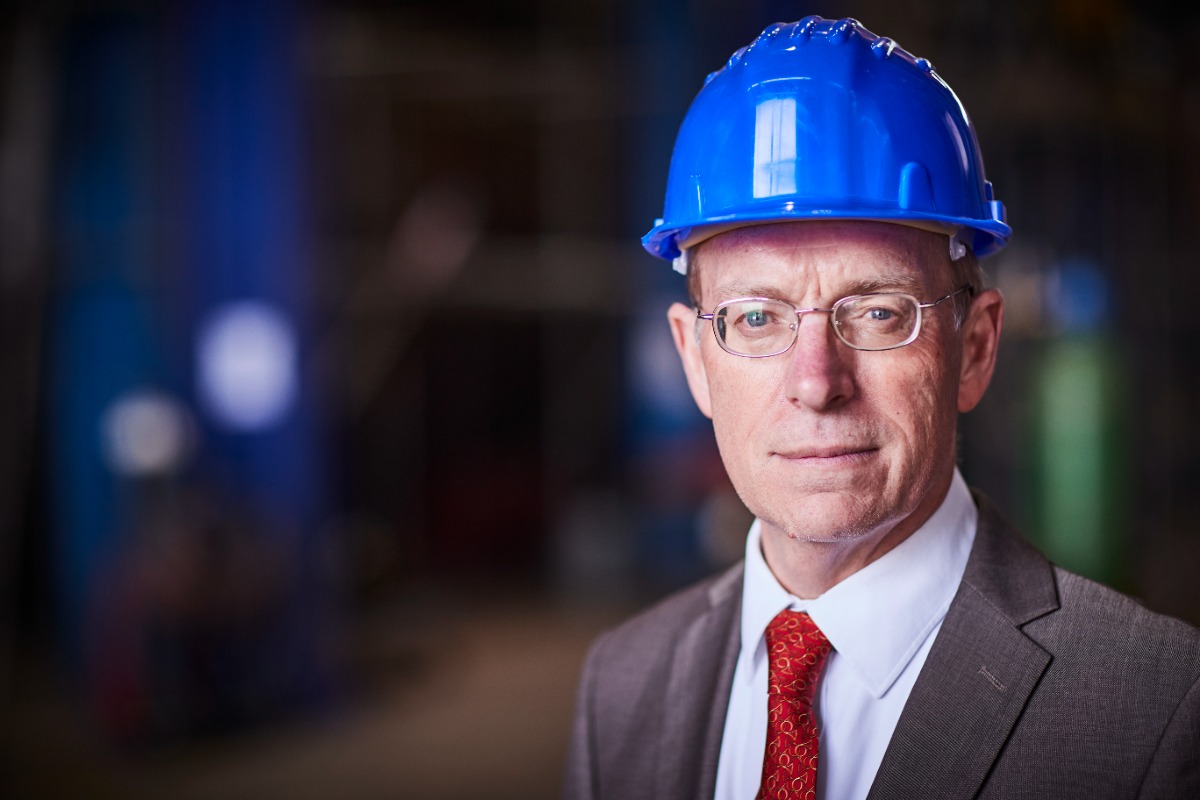
Streamlining & safety: What the chemical sector can learn from civil nuclear manufacturing processes
Submitted by:
Andrew Warmington
Julian Vance Daniel, director at Vessco Engineering, examines how the processes and procedures that govern engineering and manufacturing in the stringent civil nuclear sector could equally apply to the chemical sector
As digitisation, AI and information exchange speed up, so too do the learnings from one industry to another. Fabrication plays a crucial role in the chemical manufacturing industry and encompasses various processes involved in transforming raw materials into final products with specific characteristics.
Not only does quality fabrication enable the production of custom-designed equipment, such as reactors, distillation columns and storage tanks, these specialised components are also tailored to meet the unique requirements of chemical processes, ensuring efficient operation and optimal performance. In addition, fabrication in the chemicals sector involves the creation of unique intricate and precise systems, such as piping networks, valves and instrumentation. These components ensure the safe and controlled movement of raw materials, intermediates, and final products throughout the manufacturing facility.
Vessco is a fabricator of some of the largest vessels for the nuclear and oil and gas industries. From the transfer of knowledge and the understanding of processes, it has gained directly from its experience in these ultra-safety-regulated sectors, and can pass on and apply quality processes and enhancements in other market sector applications.
We have worked with global multinationals such as Syngenta, Sabic and Huntsman, across industries including agrochemicals. The IP and enhanced processes that we have garnered from working within the highly regulated nuclear sector have directly shaped our work in other industries, such as the water utilities, as well as the oil and gas sectors. Our experience of this is also consistent with other suppliers across the Tier 2 and Tier 3 nuclear supply chain.
Learnings from the nuclear sector
First and foremost, the civil nuclear sector is governed by some of the most stringent and rigorous documentation and processes of any industry. A serious accident in the nuclear sector is significantly worse than in others.
For that reason, the tried and tested methodologies deployed can be useful elsewhere, especially where safety and risk are critical considerations as they are in the chemical sector. Quality plans and inspection and test plans are extensive, shaping wider areas of the manufacturing workflow.
I believe that those who are involved in manufacturing and engineering within chemical sector have everything to gain by embedding some of this thinking into their own processes, starting with design, right through to inspection and quality control. Vessels are proportionately more expensive to manufacture for chemicals because of the greatly increased number of nozzles they need, for example. Meanwhile, there are more jacketed vessels and perhaps uniquely, vessels are often manufactured to have more than one use.
In nuclear engineering there is a highly developed focus on identification of counterfeit, fraudulent or suspect (CFSI) items. Proving and validating materials and parts is critical to safety assurance. It is not just about the potential problems of the purchased materials, but also about maintaining tight traceability throughout the complete manufacturing journey – such as documented evidence that the material you legitimately procured is still the same material, from the same source, should that material need to be divided across separate components.
To mitigate the risk of CFSI, both the civil nuclear and oil and gas industries rely on strict materials sourcing and QC protocols. This includes the use of trusted suppliers, strict inspections, and detailed documentation of materials and components. Furthermore, they must be able to identify these items using a variety of methods, such as physical and chemical testing, electronic tracking and traceability, and global certification programmes such as CFSI and BS EN 4872.
Is health and safety a barrier to change?
Components in the chemicals sector are not without their own strictly controlled quality and safety requirements, not just in the protection of valuable resources but in terms of the risk to the environment in the event of a major leak or breakdown. Controlled welding and monitoring techniques are crucial to meeting these standards, from the manufacture of storage vessels, or vessels that need to withstand immense pressures, temperatures or weights.
Moreover, structures and equipment used in the industry must have a long lifespan, welding being critical to durability and resilience. Having said this, it is also my experience that both the nuclear and chemical sectors are still relatively slow at embracing new technologies, such as modern methods of welding and fabrication, such as synergic MIG welding, which is proven in so many other sectors.
This has a relatively low defect rate and could, I believe, be employed more widely for the fabrication and manufacture of pressure vessels, heat exchanges and columns. However, it all comes back to safety and with change comes perceived increased risk.
Speed is crucial in industries that involve production. It is imperative that sufficient time is given for the advance preparation of documentation prior to manufacturing. The process should be precise with no room for misinterpretation.
It is, of course, true that there will be more inspection hold and witness points in civil nuclear work than in the chemicals industry, but the outcome should still be the same, and the preparation and navigation of documentation should be accounted for at the very outset to help create efficiencies, and ultimately, profitability of workflow. There is a constant requirement for innovation across all the sectors we are fortunate to work in, not least to ensure these traditionally slow processes are sped up because of the traceability and auditing of safety.
Fabrication supports innovation and process optimisation by providing opportunities for R&D. It allows manufacturers to experiment with new materials, test prototypes, and explore novel manufacturing techniques, ultimately leading to improved products and enhanced efficiency – as we have witnessed within the civil nuclear realm. Manufacturers can enhance their processes, maximise productivity and maintain a competitive edge in the dynamic and evolving chemical industry.
Likewise there is the requirement to produce components faster and more economically without detriment to quality, and if learnings from doing so can be shared with in other manufacturing realms, such as chemicals, that has got to be good for engineering, not least at a time when production and consumption is undergoing so much geo-political and economic change.