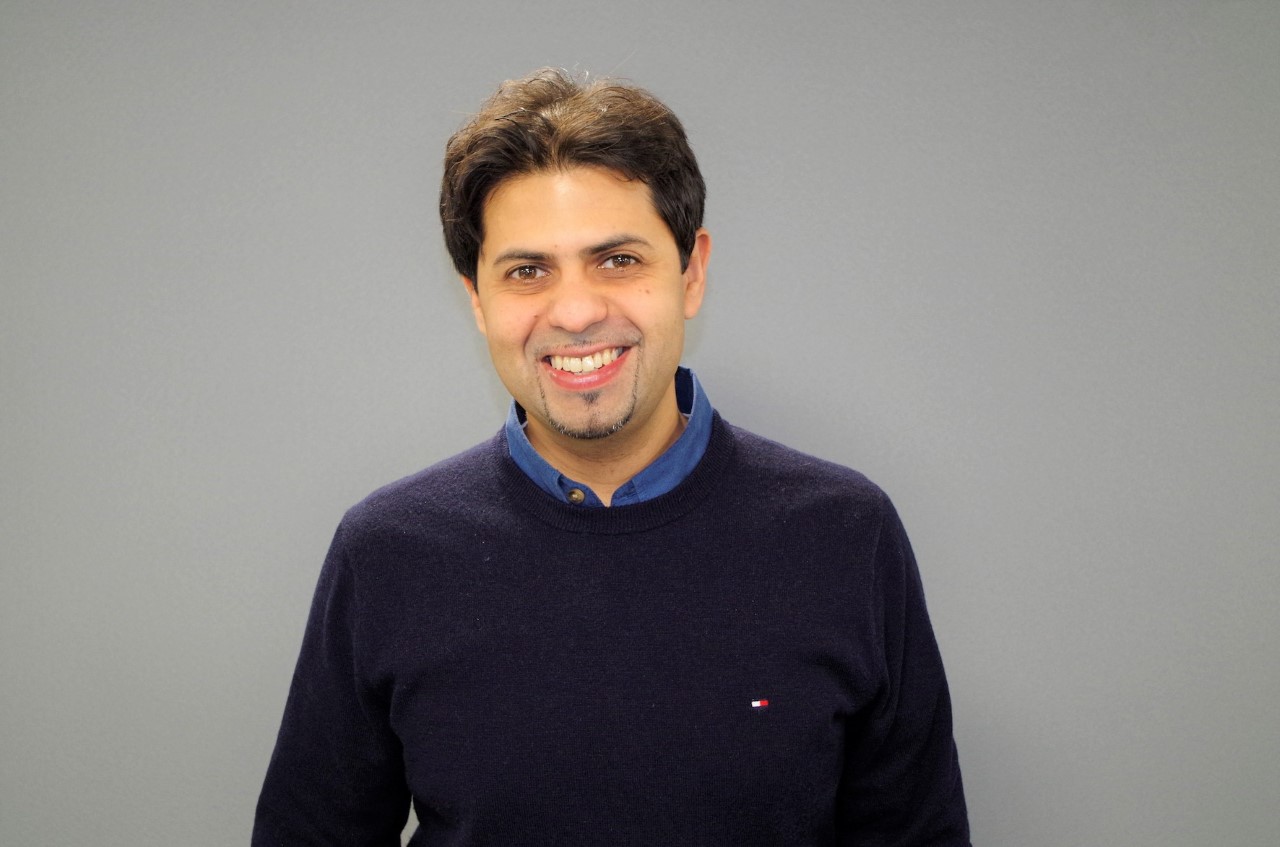
Why low accuracy chemical dosing is money down the drain
Submitted by:
Andrew Warmington
Adeel Hassan, product manager at Watson-Marlow Fluid Technology Solutions, shares some examples of how accurate chemical dosing can save costs in multiple industries
Companies in the process industries sector — from wastewater treatment providers to metal and mining or pulp and paper plants — face an extremely challenging operating climate in 2022 and beyond. Around the world, authorities are tightening the environmental regulations that govern chemical usage and disposal in process and wastewater treatment.
Energy consumption is also in the spotlight as businesses strive to meet sustainability goals and simultaneously tackle a serious energy crisis. Against a backdrop of increasing economic uncertainty, cost control is key. Now more than ever, chemical and energy savings can help make the difference when it comes to staying competitive in a global market. But when one factors in the pressure to modernise and increase capacity, it is hard for operators to know where to focus to meet obligations and make the necessary efficiencies.
Exploring the impact of the challenges that lie ahead is key to understanding the important role accurate chemical dosing can play in optimising and driving efficiencies in the use of both energy and expensive treatment chemicals. How can accuracy and reliability help businesses in the process industries sector keep their competitive edge in response to such challenging market conditions?
Chemical use up close
As wastewater treatment facilities in both the municipal and industrial sectors look to upgrade equipment to meet rising demands, European Council Directive 91/271/EEC on urban wastewater treatment is also set to change in the months ahead. It is expected that the revised directive will impose stricter discharge limits resulting in a need for increased treatment in industrial and municipal facilities.
Regulations aside, we are all now acutely aware of the impact of climate change. Society needs to reduce waste in all its forms, and it is incumbent on operators and suppliers like Watson-Marlow, which manufactures niche peristaltic pumps and associated fluid path technologies for the life sciences and process industries, to prevent the waste of chemicals.
A common metal and mining or pulp and paper plant has a capacity of around 500 m3/hr and consumes around 0.5% chemicals in the form of flocculants and coagulants. In the municipal sector, average capacity is 5,000 m3/hr or even higher. Thousands of litres of chemicals are used each day across these facilities. Inaccurate dosing can cost an operator tens of thousands of Euros in wastage and fines — not to mention irreparable damage to the environment and their reputation. Accuracy and repeatability of chemical dosing pumps is therefore critical.
An unfortunate fact is that dosing pumps’ accuracy is still unregulated, but the incoming EU regulations should be accompanied by a strong push from the industry to change that, perhaps in line with the European Measurement Instrument Directives. Long-term tests conducted at a state-of-the-art research facility in Europe show that peristaltic pumps like those in Watson Marlow’s Qdos range offer 1% accuracy with an excellent 0.5% repeatability in dosing. Results like this demonstrate that selecting the right pump can make a huge difference when it comes to chemical savings.
Energy in crisis
In parallel with changes to regulation, the European energy crisis linked to the Ukraine conflict, which is driving the highly inflated energy prices we see at present, is having a big effect on the cost of the industrial plant operation. Naturally, companies in the process industries sector are looking to make energy savings in response to both.
Peristaltic pumps like those in the Qdos range, established in the market for a decade, are low maintenance, have a long product life and do not require pulsation dampeners, degassing valves, back-pressure valves and float switches. All these elements help operators to save on not only capital expenditure and maintenance, but also energy costs.
Furthermore, high accuracy enables the use of more concentrated chemicals and smaller, more efficient dosing systems — which in turn reduce both energy and transport costs. With sustainability front of mind, we are planning a study which will help us partner with customers and calculate the amount of CO2 they can save just by choosing the right pump for their application.
Efficiency gains through accuracy
Putting this into context, the installation of a Qdos 120 peristaltic dosing pump has demonstrated that the deployment of accurate chemical dosing technologies at paper mills can deliver a significant reduction in energy usage and greenhouse gas emissions. Trials, which took place at the Netherlands-based research facility of a major supplier of food and drink packaging, led to a 3% reduction in gas consumption and 3% reduction in greenhouse gas emissions.
In wastewater treatment, a plant serving the town of Hessisch-Lichtenau in Germany was able to meet strict environmental discharge limits through accurate and reliable ferric chloride sulphate dosing. With the help of the Qdos Conveying Wave Technology pump, the Fürstenhagen plant achieved a 97.5% reduction in phosphorus load over the course of a year.
The challenges of meeting regulatory standards, striving for sustainability in the face of climate change and navigating economic uncertainty are complex and many. However, accurate chemical dosing can help companies in the process industries sector meet these challenges head on. The chemical and energy savings to be made by choosing the right pump should not be underestimated and will help businesses to run their operations with greater precision, efficiency and cost control.
Contact:
Lauren Gill
Global PR Manager
Watson-Marlow Fluid Technology Solutions
[email protected] www.wmfts.com