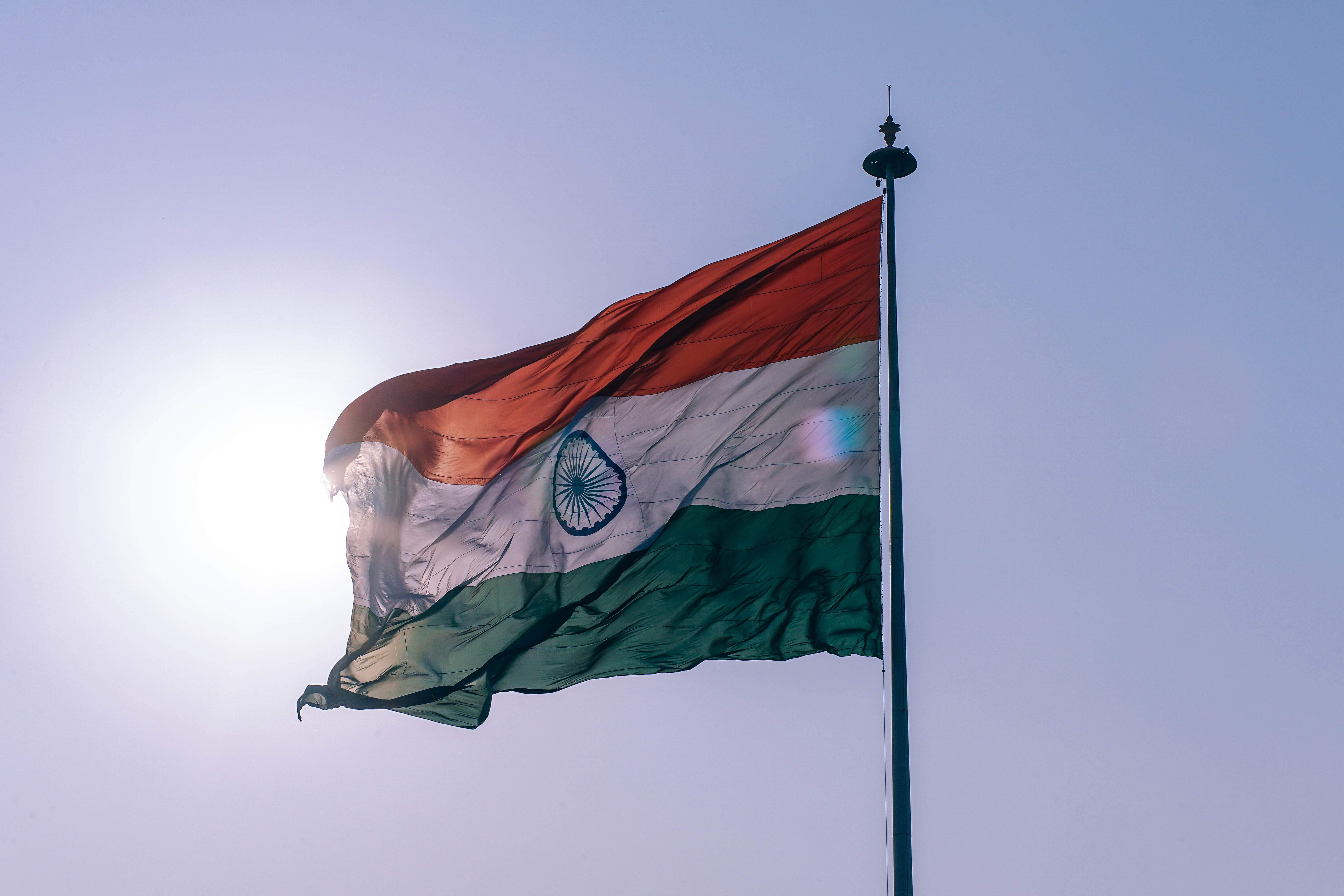
Riding high on the winds of change: India
Submitted by:
Andrew Warmington
The Indian chemicals industry, with a market size of US$145 billion is the seventh largest producer of chemicals worldwide and the third largest producer in Asia after China and Japan. Increase in domestic consumption has fuelled the growth of the speciality chemical industry in recent years to record CAGR of 14% over the past five years. The market is expected to reach US$70 billion by 2020, according to the Chemical Industry Achievement report 2016.
As the industry holds on to undeterred optimism in an environment of ambiguity and complexity, India correspondent Savita V Jayaram delves into the chaos and disruption experienced in an aftermath of new regulatory reforms, governance and SOPs that impact companies grappling with change.
Understanding the trend shift
There have been recent reports of facilities in China closing due to strict implementation of environmental standards. Furthermore, China’s slowdown and protective sentiments across the globe have made survival tougher for multinational corporations. These changes in China present opportunities for companies in India to scale up and grow.
Many companies are looking at new markets through mergers and acquisitions (M&As), by buying product lines that complement their existing offerings, aligned to meet strategic business goals. Speciality chemicals accounted for 79% of M&A-deal value globally in Q3 2017, according to a report by PwC.
Another emerging trend is the amount of R&D activity outsourced to third parties by chemical companies. While outsourced R&D can operate independently, companies need to ensure that the communication channels and stakeholder linkages with partners are strong.
Bottlenecks, challenges and opportunities for growth
Changes in regulatory policies have stirred a nationwide-debate on what works best in this volatile economy to understand customer demands, preferences and shifts in market trends.
Shedding light on the issue, Shashi Menon, director, Indenta Chemicals India, said: “Currently there is a proliferation of standards worldwide, and companies from underdeveloped and emerging economies face problems in complying with these standards. The marginal cost of certification and accreditation also places pressure on company profits in industrialised countries. The combined impact calls for strategies that revalue cost and efficacy of the current certification and accreditation system. For example, regulators could offer subsidies in certification costs.”
Focusing on other impediments to growth, Satish Wagh, chairman of Chemexcil, thinks: “Inverted duty structures, suspension of GSP benefit (on both organic and inorganic chemicals) by the EU to make our products non-competitive, reduction in incentives under chapter 3, trade remedy measures against Indian exports in Brazil and China, all need a fix. India is also facing intense competition from Chinese exporters, who are enjoying much higher incentives in their country, while the ASEAN Free Trade Agreement (FTA) has put Indian manufacturers at a serious disadvantage.”
Investments in R&D: expansion and diversification
While the industry has seen no blockbuster inventions in the past three decades, there has been a shift in innovation strategy to focus on customer-led applications development.
Dai-Ichi India is investing 160 crores in three major plant manufacturing sections, an in-house R&D centre, QC lab and a state-of-the-art ETP facility at Dahej. The expansion, which is aimed at doubling production capacity, is expected to be up and running by Q1 2018. It will focus on three key areas – oilfield chemicals, the agrichemicals sector and construction.
"We are investing in state-of-the-art technology, specifically for our EO plant. The BUSS double loop reactor can manufacture a wide range of products in a highly efficient manner. It allows for flexibility of making a variety of EO/PO products with small to large batch sizes. The efficiencies achieved by deploying a BUSS reactor will give us a competitive advantage," says Meher Taff, chief operating officer, Dai-Ichi India. “We will be moving out of our Pune headquartered facility to Dahej in a phase-wise manner … During the transition phase, both of our plants will be running simultaneously to ensure none of our customers face supply issues and that their needs are prioritised.”
“With regards to oilfield chemicals, Dai-Ichi India is in partnership with Nalco Champion to generate organic natural demand from customers. The company is also focused on introducing novel agrichemical products. In construction chemicals, the Make in India push for infrastructure development has set the stage to provide ample opportunities for growth,” Shernaz F Vakil, chairperson and managing director of Dai-Ichi India explains. "We are also tapping the export potential in the oilfield chemicals sector over the next two years.”
Anurag Jain, president and CEO (Speciality Chemical Business) at SRF also talks about expansion plans: “We plan to invest US$250-300 million in the next three to five years in the chemicals segment. Sustainable technologies are key to the future. We will continue to invest in clean, lean and green technologies to continue our growth trajectory. Last year, we invested US$100 million in a new multipurpose facility to manufacture speciality chemicals of a variety of reaction sets with a flexible production schedule, set as per customer requirements. We have also invested in a cGMP plant at Dahej to help businesses with supply of high-end pharma molecules.”
Indenta Group is focused on four verticals of business. The company is involved in manufacturing sodium hydroxide and potassium hydroxide pellets. “Also, we ventured into the laboratory chemicals business a few years back and are exporting to multiple countries. The third vertical is the business of 100% natural essential oils and natural identical oils. We are also into global sourcing of fine chemicals, pharmaceutical intermediates, fragrance and flavour ingredients, micro waxes and allied product lines … We plan to venture into the B2C segment, by launching a range of dietary supplements and wellness products. We also plan to scale up the manufacturing of reagents by introducing pharmacopoeia standard multicompendial products,” Menon says.
Impact and implications of GST
“The Goods and Services Tax [GST] is a critical change that the industry has been waiting for. Even on a global scale, the industry is keeping an active watch on the growth and revenue of companies. In the chemical industry, the government has kept a large number of items under the 18% tax slab, while those under the nil and 5% category could bring in good momentum. From an imports perspective, there would be no impact on levy of basic customs, anti-dumping or safeguard duties,” Menon added.
According to Wagh, “Post-GST, the utility of Merchandise Exports from India Scheme (MEIS) has been reduced as it can be used only for bulk chemical distribution, anti-dumping duty, safeguarding etc. It cannot be used for paying IGST. Besides, IGST is applicable on imports against Advance Authorisation, reducing their utility. Though input credit will be available later, liquidity will be an issue. IGST payable on purchases by merchant exporters as the CT1 facility is not available. Even though custom duty has remained unchanged, there has been a reduction in All Industry Rates (AIR) Duty drawback from 1.9-1.5%.”
As one of the leading businesses focused on the manufacturing of high-performance specialty chemicals, Dai-Ichi India’s offerings include paints and coatings, textiles, construction and oilfield chemicals. Introduction of GST in July this year brought “initial minor hiccups”, as Vakil explains. To get the source codes right, acquiring the GST numbers from suppliers and customers was difficult. “However, after growing pains, we are fully online with GST smooth implications on SAP.”
Transforming India into an R&D hub
The Modi government launched the 'Make in India' program in 2014, an ambitious move to make India the next manufacturing superpower. Chemicals are among the top 25 thrust sectors identified as being poised for growth.
To increase the global competitiveness of domestic chemical manufacturing industry, Wagh stresses “the urgent need to build safe transportation, storage, and shipment of hazardous chemicals, need to reduce transaction costs and ensure adequate availability of power and water to support envisaged chemical industry growth.”
“Lower cost of operations and ease of doing business is a critical success factor for the Make in India initiative to be successful. It is important for the government to focus on key issues like availability of land at favourable rates, low cost of funds for investment and robust infrastructure to make the low-cost manufacturing sustainable – the key pillar to the success of the ‘Make in India’ plan,” Jain from SRF suggests. “As the world inches towards Industry 4.0, the current investments in infrastructure in the country should be in line with future needs. Because technologies are becoming obsolete at a rapid pace, delays in investment, setting up infra and logistic facilities could hamper the success rate of this great initiative.”
Dai-Ichi India is driven by sustainable manufacturing. "All the technology that we have set up at Dahej is driven by sustainability. We have the opportunity to redesign a plant with more automation and have taken advantage of the fact. Our plants are fully or semi-automated, controlled and monitored by a DCS system. We have also invested in the latest ETP technology for our new plant," Meher Taff added.
The future industry outlook
With uncertainty the norm, companies are required to revamp their product and service offerings, implement sales training and systems to improve sales force efficiency, beef up transparency in pricing of products, invest in R&D and IT infrastructure, recruit and retain key talent to drive sustainable competitive business advantage. Companies are keen on capturing the digitalisation wave by the commoditisation of speciality chemical products through platforms such as Alibaba.
While digitalisation, on the one hand, offers next-step improvements in production process productivity and selling, general and administration (SG&A) cutbacks, there are threats buried deep in the marketplace where few chemical companies currently dare to tread.
“It is the need of the hour that Indian chemical manufacturers understand and address issues around raw materials, infrastructure and environment, product portfolio, duty structures, human resources, etc., to succeed in the competitive environment. The industry overall should adopt eco-friendly technologies for sustainable development and increase its spending on R&D,” Wagh asserts.